Keine Chance für korrosiven Flüssigdünger
Keine Chance für korrosiven Flüssigdünger
Ein dauerhafter Betrieb von Bodenbearbeitungs- und Sämaschinen ist die Voraussetzung für ein zeiteffizientes und ertragreiches Wirtschaften in der Landwirtschaft. Wichtige Bedingung: Die Maschinen müssen korrosionsbeständig gegenüber Dünger, Regen und Frost sein. Das gilt besonders für funktionskritische Verbindungsteile der Maschinenhydraulik. Wenn das Bauteil nicht optimal auf die Systemanforderungen abgestimmt oder falsch montiert ist, treten hier schnell Leckagen auf.
Die Landwirtschaft ist geprägt von Preisdruck: Betriebe müssen eine hohe Arbeitsproduktivität erreichen – zusätzlich erfordern Umweltauflagen der Europäischen Union ein ressourcenschonendes Bewirtschaften des ländlichen Raums. Einer der führenden Hersteller anforderungsgerechter Maschinen und fortschrittlicher Komponenten für die Bodenbearbeitung, Sätechnik und den Pflanzenschutz ist die Horsch Maschinen GmbH.
Neue Qualitätsstandards in der Hydraulik
Innerhalb der letzten Jahre verzeichnete Horsch einen zunehmenden Bedarf an Düngemaschinen – hier sind die Anforderungen an den Korrosionsschutz der verbauten Teile besonders hoch. „Die Korrosionsbeständigkeit gegen Flüssigdünger und Düngerstaub ist extrem wichtig für unsere Kunden. Sie erwarten einsatzsichere, aber auch optisch einwandfreie Maschinen – und das selbst noch nach Jahren des Betriebs“, betont Thomas Prüll aus der Forschung und Entwicklung bei Horsch. Um Kunden auch in der Fluidtechnik einen zukunftssicheren und gleichbleibend hohen Standard zu gewährleisten, erklärte Horsch die VOSS Fluid GmbH zum Standardzulieferer für die hydraulische Verbindungstechnik. „VOSS Fluid überzeugte uns mit der Zink-Nickel-Beschichtung, die mit ihrem hohen Korrosionsschutz am Markt maßgebend ist“, begründet Thomas Prüll.
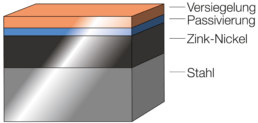
"VOSS Fluid überzeugte uns mit der Zink-Nickel-Beschichtung, die mit ihrem hohen Korrosionsschutz am Markt maßgebend ist."
– Thomas Prüll | Forschung und Entwicklung Hirsch Maschinen GmbH
Ausschlaggebende Argumente für Horsch: VOSS coat übertrifft sogar die höchste Korrosionsschutzklasse K5 des VDMA-Einheitsblattes 24576, in dem eine Rotrostbeständigkeit der Oberfläche von mindestens 720 Stunden gefordert wird. Zudem bildet sich, anders als bei reinen Zinkoberflächen, anstelle von ausgeprägtem Weißrost nur ein leichter, optisch unauffälliger Grauschleier. Mit VOSS coat beschichtete, unmontierte Teile erzielen im Salzsprühnebeltest eine Korrosionsbeständigkeit von mehr als 2.000 Stunden. Aber auch im Praxistest unter realen Bedingungen stellt die Oberfläche ihre hohe Beständigkeit unter Beweis. Dafür durchlief Zufallsware aus der laufenden Produktion die typischen Arbeitsprozesse vom Transport über die Lagerung bis zur Montage mit handelsüblichen Werkzeugen. Trotz mechanischer Beanspruchung zeigte sich an den Verbindungsteilen auch nach 1.000 Stunden keine Grundmetallkorrosion. Um sich der nachhaltigen Eignung auch bezüglich der Anforderungen in der Agrartechnik zu versichern, nahm Horsch VOSS coat genauer unter die Lupe. „Die Ergebnisse aus dem Salzsprühnebeltest sind für uns nur bedingt aussagekräftig“, so Prüll. „Die tatsächlichen Auswirkungen von Montage, Dünger, Temperatur und Feuchtigkeit auf die Korrosionsbeständigkeit zeigen sich erst auf dem Acker.“ Die Bedingungen im Einsatz stellen sogar einen wirkungsvollen Korrosionsschutz auf die Probe: Kommen freiliegende Teile in Kontakt mit Mineral- oder Nitratdüngern, kann dies zu verstärkter Korrosion führen.
Daher prüfen die Entwickler von Horsch in einem eigenen Bewitterungstest seit November 2013, wie sich Verschraubungen verschiedener Hersteller und unterschiedliche Oberflächen über einen längeren Zeitraum verhalten. Um die Praxisbedingungen realistisch nachzubilden, montierte Horsch die Verschraubungen, befestigte sie an einem Gestell und setzte sie der natürlichen Bewitterung aus. Über zwei Monate besprühten die Entwickler die Bauteile jeden Werktag mit einer gängigen und für ihre korrodierende Wirkung bekannten Flüssigdüngerlösung. Den Vergleich traten Bauteile mit A3C-Beschichtung und Zink-Nickel-Oberfläche sowie Verbindungsstücke aus Edelstahl an. Schon nach kurzer Zeit zeigte sich auf den verzinkten, gelbchromatierten Oberflächen und den handelsüblichen Zink-Nickel-Beschichtungen ganzflächig Rotrost. Auf der Verbindungstechnik von VOSS Fluid sind dagegen auch sechs Monate nach Testbeginn nur marginale Spuren von Korrosion zu erkennen. Damit schneidet VOSS coat im direkten Vergleich mit anderen Zink-Nickel-Oberflächen am besten ab – ein Hinweis darauf, dass die hohe Korrosionsbeständigkeit nicht allein auf die Beschichtung zurückzuführen ist. Das Resultat: Die VOSS Rohrverbindungen sind auch unter realen Bedingungen dauerhaft funktionsfähig und gleichzeitig eine wirtschaftliche Alternative zu Edelstahl.
Hohe Fertigungs- und Anwendungskompetenz
Der hohe Korrosionsschutz der Verschraubungen ist begründet in der von VOSS Fluid eigens entwickelten, nachhaltigen Oberflächentechnologie und der langjährigen Erfahrung in der Produktion und Anwendung von Rohrverbindungen. Der Schichtaufbau von VOSS coat ist auf den ersten Blick vergleichbar mit marktüblichen Zink-Nickel-Beschichtungen. Er besteht aus einer Zink-Nickel-Basisschicht, die anschließend passiviert und versiegelt wird. Zentrales Unterscheidungsmerkmal ist die Gestaltung der Beschichtungsprozesse, die der Hersteller aus Wipperfürth kontinuierlich optimiert:
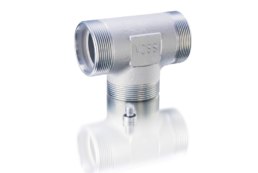
Voraussetzung ist die eigene Galvanik, in der nur Rohrverschraubungen beschichtet werden. So hat sich der Verbindungsexperte auf die effiziente und schonende Reproduzierbarkeit jedes seiner rund 16.000 Artikel spezialisiert – mehr als hundert Millionen Teile laufen jährlich durch die Galvanik. Dank der eigens für jedes Produkt hinterlegten Prozessparameter erreicht VOSS hochwertige Ergebnisse hinsichtlich einer gleichmäßigen Schichtverteilung, der Optik und der Reibbeiwerte. Schulungen zur leckagefreien Montage der Verbindungstechnik gewährleisten Horsch zusätzlich einen prozesssicheren Einbau ins Hydrauliksystem. Reklamationen in Bezug auf die Verschraubung gehören seit dem Wechsel zu VOSS Fluid der Vergangenheit an.
In der Verbindung liegt die Kraft
In der Verbindung liegt die Kraft
Was haben Medizinprodukte und Autos gemeinsam? Beides sind Hightechentwicklungen, die ohne hochpräzise gefertigte Bauteile nicht funktionieren. Möglich ist eine solch genaue Bearbeitung mit den Werkzeugmaschinen der GROB-Gruppe. Bei der spanenden Fertigung wirken extrem hohe Kräfte auf die Werkstücke ein. Sämtliche Vorrichtungen für die Werkzeug- und Werkstückspannungen werden daher mit einer ausgefeilten Hydraulik betrieben. Bei den Hydraulikverbindungen vertraut GROB auf das Rohrumformsystem VOSSFormSQR in Kombination mit der prozesssicheren Umformmaschine VOSSForm 100. Darüber hinaus setzt das Unternehmen weitere Komponenten von VOSS Fluid ein, wie leckagesichere Schneidringverschraubungen.
Der Name GROB steht international für Werkzeugmaschinen höchster Präzision. In der Automobilindustrie, im Flugzeugbau, in der Medizintechnik und in einer Reihe weiterer Branchen genießt das Familienunternehmen mit Sitz in Mindelheim großes Vertrauen. Das Produktportfolio gliedert sich in die Bereiche Systemmaschinen, Universalmaschinen für die spanende Bearbeitung, Anlagen für die Elektromobilität, komplette Montageanlagen, bestehend aus modular aufgebauten Bearbeitungszentren und Sondermaschinen, sowie den Bereich neue Technologien. Weltweit erwirtschaftet die GROB-Gruppe mit knapp 6.000 Mitarbeitern auf vier Kontinenten einen Umsatz von rund 1,3 Mrd. Euro. „Wir stellen hohe Anforderungen an uns selbst und haben den Anspruch, die Nummer 1 zu sein. Das erfordert ständige technische Innovationen. Genau das Gleiche erwarten wir auch von unseren Zulieferern“, erläutert Anton Kuhn, Abteilungsleiter Fluid-Konstruktion bei GROB.
Universalmaschinen von GROB
GROB 5-Achs Universalmaschinen lassen sich in den unterschiedlichsten Bereichen einsetzen – wie beispielsweise dem Formen- und Prototypenbau mit anspruchsvollen, hochgenauen Geometrien mit Raumschrägen und Raumbohrungen. Die Werkzeugmaschinen arbeiten auf einen tausendstel Millimeter genau. Eine solch exakte Bearbeitung setzt voraus, dass die Werkstücke in komplexen Spannvorrichtungen positioniert und fixiert werden. Dabei kommt der Hydraulik eine besondere Bedeutung zu. Sie hat die Aufgabe, Werkzeuge zu spannen und Gewichte auszugleichen. Außerdem sorgt sie für die Klemmung von Achsen und Spindeln. In der Regel wirken bis zu 120 bar auf die Hydraulikverbindungen, bei Druckspitzen vereinzelt sogar bis zu 300 bar. Rund 70 bis 100 m Hydraulikleitung sind in den Werkzeugmaschinen der G-Reihe verbaut, hinzu kommen unzählige Verbindungen. Gemäß den von GROB definierten Qualitätsstandards müssen die Verbindungselemente zwischen den einzelnen Hydraulikrohren höchste Leckagesicherheit aufweisen. „Die Hydraulik ist ein sensibler Bestandteil unserer Werkzeugmaschinen, denn hydraulische Antriebe sorgen für höchste Präzision bei den Werkzeugbewegungen. Daher muss die Verbindungstechnik zuverlässig und dauerhaft leckagefrei sein“, betont Kuhn. Neben der Leckagefreiheit sind eine einfache Handhabung und ein attraktives Preis-Leistungs-Verhältnis weitere Anforderungen, die GROB an seine Lieferanten von Hydraulikverbindungen stellt.
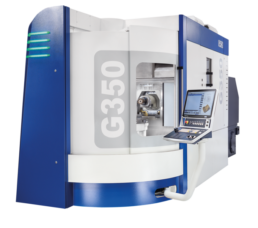
Einfach leckagefrei
Mehrheitlich setzt GROB die Verbindungslösung VOSSFormSQR ein. Neben der Qualität war die einfache Handhabung von VOSSFormSQR ein ausschlaggebender Grund. Um eine sichere Verbindung zu erzeugen, sind nur wenige Arbeitsschritte erforderlich: Zunächst formt die Umformmaschine VOSSForm 100 binnen wenigen Sekunden an das Ende eines Hydraulikrohres eine 24° Rohrkontur an. Dazu muss das Rohrende bis zur Anschlagplatte in die Maschine geschoben werden. Da ein Innendorn am Ende des Stauchkopfes die Einschnürung des Rohres verhindert, bleibt der Rohrinnendurchmesser vollständig erhalten und Druckverluste durch Einwölbungen werden verhindert.
Zusammen mit einer Weichdichtung aus FKM und einer spezifischen SQR-Funktionsmutter entsteht eine einfache und hochwertige Verbindung. Besonders die Montagesicherheit durch den Schutz vor Übermontage ist für GROB ein entscheidender Vorteil des Systems: Bei der Endmontage schlägt die Stirnseite des mit VOSSFormSQR umgeformten Rohrendes gegen den Stutzengrund im Verschraubungskörper. Beim Anzug der Funktionsmutter werden diese Komponenten fest miteinander verspannt, wobei ein spürbarer Kraftanstieg dem Monteur das Erreichen des Montageendes signalisiert. „Ein Großteil aller auftretenden Leckagen entsteht durch falsche Montage. Mit VOSSFormSQR reduzieren wir dieses Risiko entscheidend. Deshalb ist diese Technik unserer Ansicht nach die sicherste und beste Verbindung. Auch unsere Mitarbeiter sind mit dem System zufrieden“, sagt Kuhn. Weltweit hat GROB zwölf VOSSForm 100 Umformmaschinen im Einsatz.
Weichdichtende Schneidringe
Ergänzend zur Rohrumformung mit VOSSForm 100 setzt das international agierende Familienunternehmen auch den weichdichtenden Schneidring ES-4 aus dem Hause VOSS ein. Diesen verbaut GROB insbesondere in den Systemmaschinen für die Automobilindustrie. Das Funktionsprinzip basiert auf einer Zwei-Schneiden-Technologie mit zwei zusätzlichen Weichdichtungen. Die beiden Weichdichtungen sind eine Besonderheit des ES-4: Mithilfe der vollständig spaltfrei gekammerten Weichdichtung garantiert der ES-4 auch bei einem eventuellen Nachlassen der metallischen Dichtung eine trockene und schwitzfreie Verbindung. Selbst Vibrationen hält die Verbindung auf diese Weise stand. Die spaltfreie Kammerung der Dichtung erreicht der Anwender durch die Blockmontage. Diese vermeidet, dass der Ring zu tief einschneidet – eine Übermontage wird somit verhindert.
Service und Schulungen
An seinem Partner VOSS Fluid schätzt GROB nicht nur die hohe Qualität der Produkt und deren einfache und sichere Handhabung, sondern auch den Service. „VOSS Fluid ist ein agiles Unternehmen und kundennah aufgestellt“, beschreibt Kuhn. Um die geforderten kurzen Reaktionszeiten zu gewährleisten, hält VOSS Fluid zusammen mit ihrem Premium-Vertriebs- und -Servicepartner, der Fritz Stiefel GmbH, jeweils einen Teil des benötigten Materials bereit. GROB profitiert nicht nur von hoher Termin- und Liefertreue, sondern auch von Produkt- und Montageschulungen. Gemeinsam mit ihrem Vertriebs- und Servicepartner trainiert VOSS Fluid die Monteure des Maschinenbauers regelmäßig in der korrekten Anwendung der VOSS Lösungen.
Kanban-Service durch die Stiefel GmbH
Seit mehr als 13 Jahren leistet der VOSS Fluid Partner Stiefel für GROB einen Kanban-Service. Dieser ist über ein klassisches Zwei-Kisten-System mit einer definierten Mindestfüllmenge organisiert. Dreimal pro Woche tauscht die Stiefel GmbH die Behälter aus. Einmal pro Woche ist zudem ein Fachmann aus dem Bereich der Hydrauliktechnik vor Ort und unterstützt GROB in allen Fragen zu den VOSS Lösungen. „Seit dreizehn Jahren arbeiten wir mit VOSS und Stiefel zusammen. Seitdem sind wir sehr zufrieden mit der Produktqualität und dem Service, den wir durch diese Partnerschaft erhalten. Wir wünschen uns, dass das in Zukunft so bleibt“, resümiert Kuhn.
Kleiner Ring – große Aufgabe
Kleiner Ring – große Aufgabe
In weniger als einer Minute nimmt das Spezialfahrzeug Phoenix der Goldhofer Unternehmensgruppe ein Flugzeug auf und transportiert es bei Bedarf gleich mehrere Kilometer über die Rollbahn bis ans Ziel. Dabei können auch Vibrationen entstehen, die eine maximal belastbare Rohrverbindungstechnik erfordern. Bei seinem neuen Flugzeugschlepper vertraut Goldhofer daher ausschließlich auf Komponenten von VOSS Fluid wie leckagesichere, weichdichtende Schneidringe in Kombination mit einem speziellen Vormontagegerät. Eine besondere Bedeutung im Einsatz bei Wind und Wetter und gegen aggressive Enteisungsmittel im Winter kommt zudem dem langzeitsicheren Korrosionsschutz durch die Zink-Nickel-Beschichtung VOSS coat zu.
Der Name Goldhofer steht für robuste und intelligente Transportlösungen im Schwerlast- und Spezialtransport – auf der Straße, Offroad und am Flughafen. Weit über 35.000 Fahrzeuge lieferte das Unternehmen weltweit in mehr als 160 Länder, darunter auch über 6.000 Flugzeugschlepper. Ohne sie wäre der Airport-Betrieb undenkbar, denn auch das modernste Flugzeug kann eines nicht: den Rückwärtsgang einlegen. Genau an dieser Stelle übernehmen die Goldhofer-Fahrzeuge, die die Maschinen exakt in die gewünschte Start- oder Parkposition ziehen und schieben. Brandneu auf dem Markt ist der AST-2P/X, kurz: Phoenix. Die vierte Generation der stangenlosen Flugzeugschlepper ist in der Lage, mehr als 80 Prozent aller weltweit eingesetzten Flugzeuge zu bewegen.
Dazu zählen unter anderem die neue A350 von Airbus sowie die in der Entwicklung befindliche B777X von Boeing. „Geniale Lösungen sind immer einfach. Aber einfache Lösungen zu entwickeln, ist eine große Herausforderung“, bringt es Stefan Fuchs, Vorstandsvorsitzender der Goldhofer Aktiengesellschaft, auf den Punkt. „Mit dem Phoenix wollten wir weg vom allgemeinen Trend des Over-Engineerings. Daher haben wir uns auf das Wesentliche konzentriert und uns auf höchste Verfügbarkeit, verlässliche Technik und minimalen Wartungsaufwand fokussiert.“ Das Ergebnis ist ein komplett neues, kompaktes und modulares Fahrzeugkonzept, das in Punkto Antrieb, Motor, Bremskraft und vielen weiteren Bereichen neue Maßstäbe in Funktionalität und Kundennutzen setzt.
Beispiel Aufnahmevorrichtung
Nur ein wahrer Kraftprotz kann ein voll besetztes und voll betanktes Flugzeug bewegen. Der Phoenix leistet dies, indem er das Bugrad des Flugzeuges mit den Schwenkarmen seiner Aufnahmevorrichtung umschließt, spannt und anhebt. In dieser Position zieht der Schlepper die Maschine bei Bedarf kilometerweit in der auf Flughafenarealen zugelassenen Höchstgeschwindigkeit von 32 km/h. Um das Flugzeug sicher aufzunehmen benötigt der Phoenix weniger als eine Minute – was unter Flugzugschleppern einer Rekordzeit entspricht. Doch Goldhofer ging es bei der Entwicklungsphase nicht nur um eine optimale Performance. Unter der Maßgabe des Lean-Design-Gedankens wurde die Aufnahmevorrichtung komplett neu gestaltet. Waren bei den Vorgängermodellen beispielsweise noch 14 Hydraulikzylinder im Einsatz, kommt der AST-2P/X mit acht Zylindern aus. Das übersichtliche Hydraulikschema bietet freien Zugang zu allen entscheidenden Wartungspunkten. Und entgegen dem Trend, Hydraulikrohre zunehmend durch Schläuche auszutauschen, setzt Goldhofer auf Hartverrohrung.
„Wir verzichten weitgehend auf Schläuche, weil diese sehr wartungsintensiv sind“, erläutert CEO Fuchs. „Rohre hingegen müssen nur zu Beginn vernünftig montiert werden. In Kombination mit zuverlässiger Verbindungstechnik entstehen wartungsarme, leckagefreie Systeme, die über die gesamte Lifetime-Performance unserer Fahrzeuge zuverlässig arbeiten.“ Voraussetzung ist der Einsatz qualitativ hochwertiger Komponenten. Eine besondere Rolle innerhalb des Hydrauliksystems übernimmt dabei die Rohrverbindungstechnik. Hier setzt der Spezialist für Spezialtransportfahrzeuge auf die weichdichtenden Schneidringe ES-4 der VOSS Fluid GmbH. „Unserer Entscheidung für diese Technologie gingen zahlreiche Tests und Eignungsprüfungen voraus“, berichtet Fuchs. „Schließlich ist eine perfekte Hydraulik von Flugzeugschleppern das wichtigste Argument für Funktionalität und Langlebigkeit.“
Hohe Dauerfestigkeit
Die weichdichtenden Schneidringe ES-4 bieten selbst bei kontinuierlicher dynamischer Belastung die von Goldhofer geforderte dauerhafte und sichere Rohrhaltung sowie höchste Leckagesicherheit. Sie kommen an diversen Hydraulikverbindungsstellen des neuen Flugzeugschleppers zum Einsatz, unter anderem am Vormontageschild, einem entscheidenden Bauteil der Bugrad-Aufnahmeeinrichtung. Das Plus an Leckage- und Prozesssicherheit des Schneidrings ist unter anderem auf die ausgeklügelte Zweischneidentechnologie sowie die beiden integrierten Weichdichtungen zurückzuführen. Der Blockanschlag des Systems sorgt darüber hinaus für Übermontageschutz. Durch die Verteilung der Belastung auf zwei Schneiden erhält die Verbindung eine besonders hohe Dauerfestigkeit: Während die erste Schneide für den sicheren Halt des Rohres sorgt, optimiert die zweite Schneide die Ausreißsicherheit bei Druckschlägen und reduziert zudem die Gefahr von Leckagen auf ein absolutes Minimum. Der im Körper des Schneidrings integrierte Federeffekt verhindert zusätzlich Nachsetzerscheinungen, die durch Vibrationen entstehen könnten. Selbst lang anhaltende Vibrationen, wie sie beim kilometerlangen Abschleppen eines Flugzeuges entstehen können, wird auf diese Weise wirksam standgehalten.
Im Sekundärbereich des Schneidrings befinden sich zwei vollgekammerte Weichdichtungen aus FPM. Sie dichten die beiden möglichen Leckagewege zum Rohr und zum Stutzen zusätzlich ab für den Fall, dass Hydraulikflüssigkeit die metallische Dichtung überwinden sollte. Eine besonders hohe Langzeitstabilität der Elastomere gewährleistet VOSS Fluid sowohl durch die Materialauswahl als auch durch die geschützte Platzierung der gekammerten Weichdichtungen innerhalb des Schneidrings.
Prozesssichere Montage
Bezüglich der Vor- und Endmontage forderte Goldhofer maximale Prozesssicherheit. Nicht zuletzt, weil sich statistisch mehr als 90 Prozent aller Leckagen von Verschraubungen auf Fehlmontagen zurückführen lassen. Der Spezialist für Spezialtransportfahrzeuge entschied sich daher für die Anschaffung mehrerer Vormontagegeräte der neusten Generation: Der Typ 90 Comfort von VOSS Fluid arbeitet mit Fehlererkennung und automatischer Druckeinstellung. So werden fehlende oder falsch eingelegte Schneidringe schon vor der Montage identifiziert sowie Über- und Untermontagen wirksam unterbunden.
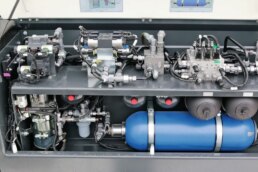
Die Monteure bei Goldhofer rüsten das Vormontagegerät lediglich mit dem passenden verschleißfesten VOSS Werkzeug, das standardmäßig mit einem RFID-Chip ausgestattet ist. Das ins Typ 90 Comfort integrierte RFID-Lesegerät liest den Chip aus und stellt die entsprechenden Montageparameter automatisch ein. Direkt im Anschluss beginnt die prozesssichere und zudem äußerst zügige Vormontage. Auch die Endmontage ist sicher gestaltet, da der ES-4 Schneidring auf Blockanschlag montiert wird. Der deutliche Kraftanstieg signalisiert dem Monteur eindeutig den Endpunkt der Montage. Zum Abschluss markiert der Goldhofer-Mitarbeiter die Verschraubung mit einem gelben Kreuz – jedes Mal ein Zeichen für eine weitere perfekte Verbindung.
Langzeitkorrosionsschutz
Da Flugzeugschlepper bei allen Wetterbedingungen zum Einsatz kommen und im Winter sogar besonders aggressiven Enteisungsmitteln ausgesetzt sind, waren die Forderungen von Goldhofer auch im Hinblick auf den Korrosionsschutz kompromisslos. „Alle unsere Systembauteile sind mit höchstem Korrosionsschutz ausgelegt. Das muß natürlich auch für die Rohrverschraubungen gelten“, berichtet Fuchs. „Damit ist das gesamte System widerstandsfähiger gegenüber mechanischer Beanspruchung und gegenüber aggressiven Medien.“ Für den neuen Phoenix bedeutet dies: Sämtliche Hydraulikleitungen sind galvanisch verzinkt und erhalten eine zusätzliche organische Schutzschicht. Und auch die Rohrverschraubungen verfügen über einen besonderen Zink-Nickel-Oberflächenschutz. Im Fall der ES-4-Schneidringe ist dies der Langzeitkorrosionsschutz VOSS coat. Er erreicht nicht nur die höchste Korrosionsbeständigkeitsklasse K5 nach dem VDMA-Einheitsblatt 24576, sondern überschreitet ebenfalls die geforderten Beständigkeitswerte gegen Weiß- und Rotrost deutlich. „Die ES-4 Schneidringe erfüllen unsere hohen Erwartungen zu einhundert Prozent“, resümiert CEO Fuchs zufrieden. „In VOSS Fluid haben wir einen absolut qualitätsorientierten Partner, auf den wir uns jederzeit verlassen können.“