Hidden Champions im Fahrzeugraum
Hidden Champions im Fahrzeugraum
Ob Automobil, Landmaschine oder Baumaschine – ohne hydraulische Verbindungstechnik versagen ihre grundlegenden Funktionen. Hydraulikleitungen sind so etwas wie die Hidden Champions im Fahrzeugraum. Weitgehend unterschätzt wird jedoch deren Optimierung auf den jeweiligen Einsatzzweck.
Sei es aus Kostengründen oder aufgrund schlechter Beratung: Der optimalen Rohrleitungsführung im Bauraum wird häufig zu wenig oder zu spät Beachtung geschenkt. Ein Fehler, den eine frühzeitige, fundierte Beratung und „Taktikschulung“ vermeiden kann.
Autor: Georg Rempel, Leiter Produktmanagement bei VOSS Fluid
In Mannschaftssportarten wie Fußball, Eishockey, Handball & Co. gibt es ein entscheidendes Element, mit der dem der Erfolg steht und fällt: die richtigen Laufwege. Sie sind der Faktor, den der Trainer vor jedem neuen Spiel überdenken und seiner Mannschaft vermitteln muss. Denn: Jeder Gegner ist anders. Kein Laufspiel ist eins zu eins kopierbar. Dieses Beispiel lässt sich übertragen: Jedes Fahrzeug ist anders und mit ihm jeder Bauraum. In hydraulischen Systemen haben Rohrleitungen die Aufgabe, die Medien zu führen. Dabei ist zu berücksichtigen, dass Rohrleitungen stets unterschiedlich verlaufen und je nach Anwendungsgebiet in unterschiedlicher Ausprägung mechanisch, korrosiv und thermisch beansprucht werden.
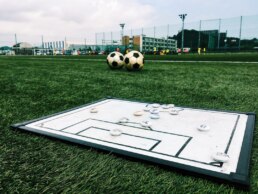
Von Herstellern solcher einbaufertiger Hydraulikleitungen werden folglich Kompetenzen in unterschiedlichsten Bereichen gefordert: angefangen vom Beratungs-Know-how über die Biege- und Einbau- bis zur Prüfkompetenz. Umso besser, wenn Hydraulikleitungen individuell auf den Bauraum zugeschnitten gefertigt und direkt einbaufertig geliefert werden. Das ist aber nur dann möglich, wenn die Rohrleitungsführung früh im Planungsprozess berücksichtigt wird und nicht erst lange nach dem Engineering des Maschinenraums. Denn je frühzeitiger die Kunden unsere Experten bei der Planung des Fahrzeugraums hinzuziehen, desto individueller können wir die zu verbauenden Rohr- und Schlauchleitungen fertigen – zugunsten von Funktionalität, Leckagesicherheit und Witterungsbeständigkeit. Zu diskutieren ist im Zuge dessen stets die Fertigung einer bereits einbaufertigen Leitung, die perfekt auf den jeweiligen Bauraum zugeschnitten ist. Ein weiterer Vorteil für den Kunden: Er kauft die gesamte Kompetenz des Entwicklers und Monteurs in Hinblick auf das Zusammenspiel aller Komponenten. Es werden keine einzelnen Komponenten verschiedener Hersteller verbaut; vielmehr erhält der Kunde ein ganzheitliches Montageprinzip, innerhalb dessen alle Komponenten perfekt aufeinander abgestimmt sind.
Die Taktik: Raumdeckung
Es geht kurz gesagt um die Kompetenz, eine einbaufertige Hydraulikleitung so individuell wie möglich auf den Kunden und dessen „Spielsituation“ anzupassen. Diese Kompetenz ist essenziell, um dem Kunden eine dauerhaft beständige Lösung zu fertigen, die perfekt an ein komplexes Maschinendesign – an den Raum – angepasst ist. Vom Aufhängesystem über Verschraubungen bis zum umgeformten Rohr kann ein solcher ganzheitlicher Beratungsansatz die gesamte Produktbreite berücksichtigen. Für uns als Berater bedeutet das: Wir können auf Basis eines vom Kunden zur Verfügung gestellten 3-D-Modells die Hydraulikleitungen einbaufertig konstruieren und verbauen. Die sinnvollere Alternative ist jedoch, sich der Komponenten und Komplexität des geplanten Bauraums schon im Erstgespräch anzunehmen und das Produktdesign entsprechend anzupassen – und von Punkt A bis Z alles so liefern, dass es auch im Hinblick auf den Einsatzzweck Sinn ergibt. Nehmen wir allein den Faktor Witterung: Ein Bagger im Steinbruch beispielsweise hat andere Anforderungen als ein Bagger, der an der Küste zum Einsatz kommt. Salzwasser greift das Material anders an als Erde und Staub. Die Komponenten müssen sich dabei nicht wesentlich unterscheiden, die Anforderungen und Umgebungsbedingungen unterscheiden sich jedoch teilweise massiv. Und das ist nur ein Faktor von vielen, den es zu berücksichtigen gibt. Hier ist eine hohe Beratungskompetenz verbunden mit einer exzellenten Kenntnis des „Spielfeldes“ gefordert.
Das Spielfeld: Der Fahrzeugraum
Dieses Spielfeld ist der Fahrzeugraum – und es ist tendenziell nicht nur kleiner als früher, es ist auch eng umstellt. Kunden fordern eine immer größere Effizienz in einem immer kleiner werdenden Bauraum. Dementsprechend höher muss die Effizienz des Hydrauliksystems sein. Dessen stetige Optimierung wird jedoch meist vernachlässigt, da es in der Regel das letzte Glied in der Kette ist. Viele Kunden setzen auf ein seit Jahren bestehendes Hydrauliksystem. Wir als Berater sind häufig in der Lage, diesen Kunden zu sagen: Schau mal, was du alles optimieren kannst, um eine nichtsdestotrotz geforderte Effizienzsteigerung zu erreichen. Oder konkret: Tausche deine Verbindungstechnik, so erreichst du eine wesentlich höhere Prozesssicherheit in der Fertigung bzw. eine höhere Leckagesicherheit und vermeidest Ausfälle beim Kunden.
Die Wahl der richtigen Verbindungstechnik ist hier grundlegend, kommt es bei einer Hydraulikleitung doch in erster Linie auf das Zusammenspiel zwischen Rohr und Verbindung an. Dementsprechend hoch sind die Ansprüche an diese Verbindungen: Sie müssen dauerhaft hohen Drücken standhalten, flexibel auf Schwingungen der Bauteile reagieren, strömungsgünstig und leckagesicher sein. Daher gilt es, die richtigen Komponenten sorgfältig auszuwählen und auf die Dimensionierung der Rohrleitungen (Werkstoff, Länge, Rohrinnendurchmesser, Wandstärke etc.) anzupassen.
Gegenpressing: Wenn der Druck steigt...
Aufgrund der permanenten Druckverhältnisse, Umwelteinflüsse, Beschädigungen und natürlicher Alterung ist die Lebensdauer von Hydraulikleitungen endlich. Die Verwendungsdauer von Schlauch- wie von Rohrleitungen hängen also im Wesentlichen von den Einsatz- und Umweltbedingungen ab. UV-Strahlung beispielsweise lässt das Schlauchmaterial schneller altern; Gummi verliert seine Elastizität und wird brüchig. Das bedeutet: Je anspruchsvoller bzw. extremer diese Bedingungen sind, desto angemessener sollten die Abstände sein, in denen die Leitungen ausgewechselt werden.
Von den äußeren Bedingungen abgesehen, kommt es auf die richtige Aufstellung aller Leitungskomponenten an. Auch hier besteht häufig Optimierungspotenzial – insbesondere dann, wenn das hydraulische System mehr leisten muss als ursprünglich vorgesehen, beispielsweise durch fortwährende, impulsartige Druckstöße, wodurch alle Komponenten extrem beansprucht werden. In diesem Fall gilt es, das System auf „den Gegner“ anzupassen. Auch aus diesem Grund werden wir von VOSS Fluid vermehrt zur Beratung bei Fremdsystemen hinzugezogen. Die grundlegende Frage in solchen Fällen: Wie kann das hydraulische System optimiert werden, um nachhaltig zu funktionieren und hohe Folgekosten zu vermeiden? Beispiele sind eine falsche Fixierung der Leitungen zur Befestigung, Fehler bei der Leitungsverlegung oder beengte Einbauverhältnisse – diese und viele weitere Aspekte beeinträchtigen die Lebensdauer der verbauten Komponenten und schränken die Effizienz der Maschine weiter ein.
Aus diesem Grund setzen wir von VOSS Fluid bei einbaufertigen Hydraulikleitungen auf den Systemgedanken: Gerade in der Zusammenarbeit mit global agierenden OEMs haben wir unser Angebot in den vergangenen Jahren auf individuell gefertigte, einbaufertige Hydraulikleitungen mit den entsprechenden Serviceleistungen dahinter ausgebaut. Ziel ist es, alle Einzelbauteile perfekt aufeinander abzustimmen, um die bestmögliche Funktionalität und Leckagesicherheit zu garantieren. Auf diese Weise erhalten unsere Kunden persönliche Beratung, individuelles Design und eine präzise Fertigung aus einer Hand.
Auf das Prinzip einbaufertiger Hydraulikleitungen sowie Rohrverschraubungen inklusive Service aus einer Hand setzt auch der langjährige VOSS-Kunde HYDREMA. Das international tätige Unternehmen entwickelt, baut und vermarktet hochtechnologische Baumaschinen. Der Hauptsitz des Konzerns und das Hauptwerk befinden sich in Støvring in der Nähe von Aalborg im Norden Dänemarks. HYDREMA produziert aber auch in Deutschland. Mit den ehemaligen Weimar-Werken in Thüringen konnte man 1996 einen bedeutenden Baggerproduzenten übernehmen. Marianne Frank Mogensen, Purchasing Manager Hydrema Group: „Hydrema hat seit vielen Jahren im Werk Støvring eine eigene Fertigung von Hydraulikrohren. Diese Fertigung wird seit 2009 mit VOSS ES-4 Schneidringen bestückt. Seit der Entscheidung, die Rohrbiegerei als Teil unserer Produktion an VOSS Fluid auszulagern, kam dies unserer Qualitätssteigerung, Fertigungstiefe und Flexibilität zugute. Wir haben hier von Tag eins an nur gute Erfahrung gemacht. Die Beratung war sehr professionell – sowohl in allen technischen wie auch in logistischen Fragen.“
Die richtige Aufstellung: Je eingespielter, desto besser...
Beim Prinzip „alles aus einer Hand“ profitiert der Kunde von einem eingespielten Team an Komponenten. Zu Beginn jedes Fertigungs- oder Optimierungsprozesses steht daher die Produktauswahl. Diese Produktauswahl ist entscheidend, um in den Fahrzeugen und Maschinen die ideale Leitungsführung und Funktionserfüllung zu gewährleisten. Neben dieser grundlegenden Beratung sollte ein detailliertes Montagetraining gleich mit im Angebot stehen. So wird nicht nur der verfügbare Bauraum optimal ausgenutzt; die persönlichen Schulungen reduzieren zudem Folgekosten für Reparaturen, Service und Instandhaltung –zugunsten einer steigenden Prozesssicherheit. Aufgrund der aufeinander zugeschnittenen Systemkomponenten stellen Fahrzeug- und Maschinenbauer einen einheitlichen Qualitätsstandard sicher, statt auf viele einzelne Insellösungen zu vertrauen. Vorsortierte Montagekits und einbaufertige Baugruppen garantieren eine direkte Verfügbarkeit aller Komponenten, was nicht nur die einzelnen Prozesse optimiert, sondern auch Lagerkosten und Wiederbeschaffungszeiten reduziert. Der Endmontageprozess wird deutlich verkürzt und ist durch das einheitliche Montagekonzept komponentenübergreifend.
Beratung-Know-how
Fertigungskompetenz
hauseigene Qualitätssicherung
Die Kombination aus Beratungs-Know-how, Fertigungskompetenz und hauseigener Qualitätssicherung führt zu einem prozesssicheren Lösungsanbieter – auch bei komplexeren Aufgabenstellungen oder individuellen Kundenwünschen. Für die Planung von einbaufertigen Hydraulikleitungen sollten diese Kompetenzen vor allem in den Bereichen Biegen, Löten, Schweißen, Krimpen und Prüfen bestehen. Da jedes Anbindungssystem individuell geplant werden muss, gilt es, jedes System individuell um- und anzuformen, anzulöten oder zu schweißen. Dazu gehört auch das standardmäßige Verschließen der Leitungsenden, die Endbearbeitung und abschließende Qualitätsprüfungen (Dichtheits- und Konturprüfungen etc.) bis hin zur individuellen Laserbeschriftung der Leitung und optischen 3D-Vermessung. Und das alles für verschiedenste Materialien und Oberflächen. Kurz gesagt: Je größer die Fertigungstiefe, desto besser das „Spielverständnis“.
In diesem Zusammenhang helfen auch vorsortierte Montagekits, wie VOSS sie seinen Kunden bereitstellt: Sie beinhalten individuell zusammengestellte Verpackungseinheiten als vorsortiertes Produktionsmaterial, jeweils passend zur aktuellen Phase des Produktionsprozesses. Für den Kunden bzw. Anwender heißt das: Er muss sich nicht um einzelne Verbindungen Gedanken machen, sondern kann das große Ganze im Blick behalten. Den Kunden bestmöglich in den Fertigungsprozess einbinden bedeutet aber auch, ihn an der Qualitätsprüfung teilhaben zu lassen. Eine Auditierung der Fertigungskette, innerhalb derer jeder einzelne Fertigungsschritt dokumentiert wird, schafft zusätzliches Vertrauen und minimiert das Fehlerpotenzial.
Fazit: Jedes Spiel ist anders
Um ein Champion zu werden bedarf es neben Erfahrung und Spielwitz, besonders der strategischen Feinplanung und einer auf die stetig neuen Anforderungen zugeschnittenen Systemjustierung. Aufgrund der extrem hohen System- und Typenvielfalt sowie hohen Qualitätsunterschieden kommt der Beratungsleistung auf dem Gebiet der hydraulischen Verbindungstechnik eine hohe Bedeutung zu. Die Einzelkomponenten des gewählten Hydrauliksystems sollten perfekt auf den jeweiligen Anwendungsfall zugeschnitten sein. Und dieser Anwendungsfall kann sich über die Jahre verändern, weshalb die Leitungen eventuell auf den neuesten Stand der Technik gebracht werden sollten. Unsere Experten verfügen über langjährige Anwendungserfahrung und haben eine entsprechend hohe Kompetenz in der Auslegung, Verlegung und Komponentenauswahl entwickelt. Bei Neuentwicklungen empfiehlt es sich, dass der Kunde so früh wie möglich einen Experten in den Entwicklungsprozess und das Prototyping mit einbindet. Denn: Jedes Spiel ist anders.
Neues Design schafft ganzheitlichen Mehrwert
Neues Design schafft ganzheitlichen Mehrwert
Für den Markterfolg von Maschinen und Anlagen sind technologische Faktoren wie Leistung, Effizienz und Funktionalität entscheidend. Wer Innovation allerdings rein technisch begreift, denkt zu kurz. Maschinen sind in zunehmendem Maß Markenbotschafter, die ihre „inneren Werte“ durch anspruchsvolles Industriedesign optisch zum Ausdruck bringen. Daher ist auch die Zulieferindustrie aufgerufen, ihre Innovationskraft zukünftig in beiden Kategorien unter Beweis zu stellen: Funktion und Form.
Genau diesem hohen Anspruch stellte sich bereits der Verbindungstechnikspezialist VOSS Fluid. Der international aufgestellte Anbieter von Rohrverbindungen für die Stationär- und Mobilhydraulik entwickelte ein neues Design für seine 24° Rohrverschraubungen – eines der meistverbreiteten Verschraubungssysteme. „Dabei ging es uns nicht nur um die Etablierung eines zukunftsweisenden Looks“, berichtet Detlef Le, Entwicklungsingenieur bei VOSS Fluid und Projektleiter der Designumstellung. „Vielmehr war es unser Ziel, unseren Kunden bei Form und Funktion echten Mehrwert zu bieten.“ Schon 2012 fällte das VOSS Fluid Management die strategische Entscheidung. Von der Umstellung waren rund 4.500 der insgesamt 16.000 Verkaufsartikel in unterschiedlichen Größen und Ausführungen betroffen, darunter Winkel‑, T- sowie L- und Kreuzverschraubungen.
Entwicklungsziele
Vier Grundsätze standen zu Beginn der zweijährigen Entwicklungsphase für VOSS Fluid fest: Zum einen sollte die Schlüsselfläche vergrößert und damit maximal kompatibel mit dem Montageschlüssel sein. Denn moderne Maschinen werden immer kompakter konstruiert, was im Hydrauliksystem zu engen Bauräumen und einer erschwerten Montage führt. Eine vergrößerte Schlüsselfläche verbessert die Montagebedingungen auch unter schwierigen Bedingungen. Trotz dieser erhöhten Funktionalität sollte bei der Entwicklung zweitens das bisherige Gewicht der Verschraubungsartikel beibehalten oder sogar gesenkt werden, um erhöhte Materialkosten auszuschließen und den Bedürfnissen des Maschinen- und Anlagenbaus nach kompakten Systemen Rechnung zu tragen. „Außerdem war es unser Anspruch, statt der x-ten Variante des marktüblichen Sechskantdesigns eine unverwechselbare Optik zu kreieren, mit der sich unsere Kunden klar von ihrem Wettbewerb distanzieren können und für internationale Märkte gerüstet sind. Schließlich fungieren Maschinen und Anlagen heute als wichtige Markenträger und die Hydrauliksysteme inklusive der verbauten Verbindungstechnik sind oftmals wichtige Elemente des visuellen Erscheinungsbildes“, erläutert Detlef Le die ehrgeizigen Designziele. Der vierte Entwicklungsschwerpunkt lag für das Unternehmen auf der Kompatibilität von Qualitätsanspruch und Serienfertigung. So sollten die neuen Verbindungskomponenten nicht nur zeit- und kosteneffizient gefertigt werden, sondern auch konstant gute Produkteigenschaften aufweisen.
Von der Idee zur wirtschaftlichen Umsetzung
„Im ersten Schritt haben wir zusammen mit dem Industriedesign eine Studie durchgeführt und mehrere Verschraubungsentwürfe auf wirtschaftliche und technische Eignung geprüft“, so Entwicklungsingenieur Le. Für eine effiziente Umsetzung differenzierte VOSS Fluid im Vorfeld die hohe Varianz der 24° Rohrverschraubungen nach Schlüsselweite, Länge, Durchmesser und Verschraubungstyp und fasste diese konstruktiv sinnvoll zusammen. Was auf dem Papier begann, nahm im 3D-CAD-Modell Gestalt an und wurde per Finite-Elemente-Methode virtuell auf Belastbarkeit überprüft. Dabei stellte das Unternehmen sicher, dass die neu gestalteten Verschraubungsartikel mindestens die marktübliche Druckstufe beibehielten. Parallel inspizierte Detlef Le mit den Kollegen aus der Zerspanung, welche Maschinen sich am besten für die Fertigung der neu gestalteten Artikel eigneten. Dann definierte das Entwicklungsteam, wie sich die Prozesse wirtschaftlich innerhalb des Gesamtbetriebs anpassen ließen – ohne das laufende Tagesgeschäft zu behindern. Ein positiver Nebeneffekt: Mit den Ergebnissen aus der Fertigungsanalyse gelang es VOSS Fluid, eine effizientere Zerspanung der neu designten Rohrverschraubungen umzusetzen. Last, but not least führte das Entwicklungsteam gemeinsam mit der hochmodernen Inhouse-Galvanik diverse Tests durch, um auch für alle neuen Ausführungen der 24° Rohrverschraubungen eine homogene Beschichtung mit dem Zink-Nickel-Korrosionsschutz VOSS coat zu gewährleisten. Dieser sorgt bei sämtlichen Produkten des Unternehmens für eine dauerhafte Korrosionsbeständigkeit, deren Schutz etwa um das Zehnfache besser ist als der von konventionell eingesetzten Zinkschichten.
Bewährungsprobe bestanden
Für die finale Entwicklungsphase wurden Prototypen aus Stahlguss gefertigt. „Nachdem wir die Praxistauglichkeit am Schraubstock nachgewiesen hatten, testeten ausgewählte Kunden – alles große Erstausrüster im Bereich Nutzfahrzeuge und Mobilhydraulik – das Modell des Verschraubungsdesigns“, schildert Detlef Le. „Auf Basis ihrer Rückmeldung haben wir letzte Verbesserungen vorgenommen.“ Insgesamt konnte VOSS Fluid die Anwenderfreundlichkeit so enorm steigern: Anders als bei marktüblichen Verbindungskomponenten liegt beispielsweise die höchste Kante des neuen Verschraubungskörpers niedriger als das Gewinde. Der Monteur profitiert so insbesondere an schwer zugänglichen Stellen von einem maximalen Spielraum beim Ansetzen des Montageschlüssels.
Gleichzeitig kam das Unternehmen dem Kundenwunsch nach einem möglichst geringen Teilegewicht nach, das trotz vergrößerter Schlüsselfläche den Marktstandard nicht überschreitet. Insgesamt stellt das neue Design der 24° Rohrverschraubungen von VOSS Fluid eine prozesssichere und hochbelastbare Lösung für den Einsatz in modernen Hydrauliksystemen dar. Mit vergrößerter Schlüsselfläche und anwendungsgerechter Kontur ermöglicht es ein optimales Montagehandling auch auf beengtem Bauraum. Hersteller von Mobil- und Stationärhydraulik profitieren von effizienten Einbauzeiten und dauerhaft leckagesicheren und optisch hochwertigen Rohrverbindungen.
Zertifizierte Produktqualität nach IACS
Zum Abschluss prüfte das Unternehmen das neue Verschraubungsdesign im werkseigenen Versuchslabor nach ISO 19879. Das Ergebnis: Sowohl die Berstdruckprüfung als auch die Druckimpulsprüfung meistert die neue Geometrie zuverlässig. Sie hält einem viermal höheren Innendruck und mindestens einer Million Lastwechsel bei pulsierender Belastung stand. Um die Tauglichkeit zusätzlich von offizieller Seite bestätigt zu bekommen, ließ VOSS Fluid das Design durch den Dachverband der weltweit namhaftesten Zertifizierungsgesellschaften (IACS) zertifizieren. Die Organisation bestätigte die hervorragende Leistungsfähigkeit der Produkte. So bestehen die neuen 24° Rohrverschraubungen zusätzlich zu den ISO-Prüfungen mindestens 500.000 Lastwechsel bei kombinierter Belastung aus Berstdruck, Druckimpuls und Biegeimpuls.
Fazit
Technologisch fortschrittlich, hochmodern und anspruchsvoll im Design – das sind zentrale Maßstäbe des Maschinen- und Anlagenbaus im Bereich der Produktentwicklung. Genau diesen Forderungen stellt sich VOSS Fluid mit ihren neuen 24° Rohrverschraubungen. Sie sind das Ergebnis einer vollumfänglichen Auseinandersetzung mit den aktuellen Bedürfnissen und zukünftigen Anforderungen der Anwenderbranchen. Und bieten damit echten Mehrwert – in Form und Funktion.
Einschneidend anders
Einschneidend anders
Die perfekte Schneidring-Rohrverschraubung ist leckage- und prozesssicher, höchst belastbar und druckbeständig, verhindert systemimmanent Fehlmontagen – und war bislang ausschließlich im Wunschdenken vieler Anwender existent. VOSS Fluid hat nun eine Lösung auf den Markt gebracht, die all diese Vorteile in einem einzigen Schneidringsystem vereint und selbst unerfahrene Monteure zu Präzisionsarbeit befähigt.
Schneidringsysteme sind Sicherheitsgaranten. In hydraulischen Anlagen sorgen sie für die leckagefreie Verbindung von Rohren. So weit zumindest die Theorie. Denn bislang war die prozesssichere Verschraubung immer auch von der Erfahrung und Konzentration des jeweiligen Monteurs abhängig. Diesem wenig zufriedenstellenden Faktum setzt VOSS Fluid nun ein montagesicheres System entgegen: den VOSSRingM mit VOSSRing-Vormontagestutzen. Die patentierte Lösung zur Verbindung von Stahl- und Edelstahlrohren ist einfach in der Handhabung und ermöglicht selbst unerfahrenem oder häufig wechselndem Personal eine punktgenaue Vor- und Endmontage.
Der Ring der Ringe
Basis der intelligenten Lösung ist der VOSSRingM. Mittels optimierter Zweischneidentechnologie gewährleistet er selbst bei dünnwandigen Rohren einen perfekten Einschnitt und einen besonders festen Sitz am Rohr. Der stabile Schneidringquerschnitt sowie weitere geometrische Details garantieren höchste Druck- und dynamische Belastbarkeit. So hält der Ring Drücken von bis zu 800 bar bei einem vierfachen Sicherheitsfaktor problemlos stand. FEM-optimierte Abrundungen am Schneidring vermindern das Risiko von Stutzenbeschädigungen und verhindern wirksam das Mitdrehen der Rohre während der Montage. „Es war unser Anspruch, einen komplett neuen Schneidring zu entwickeln, der in Summe alle relevanten Merkmale einer perfekten Rohrverbindung in sich vereint“, beschreibt Gerd Berghaus, Produktentwickler bei VOSS Fluid, die ehrgeizigen Projektziele. „Daher war es für uns selbstverständlich, auch hinsichtlich des Werkstoffs und Härteverfahrens nach dem Optimum zu forschen.“
Perfekte Materialbeschaffenheit
Im Ergebnis sollte der Schneidring zwei zunächst gegensätzliche Eigenschaften in sich vereinen: eine hohe Festigkeit für den optimalen Rohreinschnitt und um den hohen dynamischen Belastungen standzuhalten, sowie ein weiches und zähes Gefüge, um eine geringe Rückfederung nach der Montage zu ermöglichen. Dafür ließ VOSS einen Sonderwerkstoff mit einer homogenen, feinkörnigen Gefügestruktur entwickeln, der zudem zäh und bruchunempfindlich ist. Das anschließende Härteverfahren verleiht dem VOSSRingM die notwendige dünne, aber besonders harte Randschicht. „Auf diese Weise hatten wir alle Anforderungen erfüllt, die anspruchsvolle Anwender an einen Schneidringwerkstoff stellen“, resümiert Berghaus.
„Was nützt Ihnen der beste Ring, wenn die Fehlerquellen bei der Montage so vielfältig sein können wie die Menschen, die ihn einbauen?“
– Gerd Berghaus | Produktentwickler, VOSS Fluid
Prozesssichere Vormontage mit Anschlagfunktion
Mit der Fertigstellung des VOSSRingM war das Projekt jedoch längst nicht abgeschlossen. „Was nützt Ihnen der beste Ring“, so Produktentwickler Berghaus, „wenn die Fehlerquellen bei der Montage so vielfältig sein können wie die Menschen, die ihn einbauen?“ Um diese Sicherheitslücke konstruktiv zu schließen, entwickelte das Unternehmen ein höchst sicheres Montagewerkzeug: den VOSSRing-Vormontagestutzen. Die Lösung verhindert Montagefehler, indem sie dem Monteur den genauen Endpunkt der Vormontage mittels eines deutlich spürbaren Kraftanstiegs signalisiert. Dieser erwächst aus der integrierten Anschlagfunktion: Ist die Vormontage abgeschlossen, kommt der Stutzen mit einer definierten Anschlagfläche des Rings in Kontakt. Der Montageprozess wird somit am optimalen Punkt beendet – eine Übermontage ist wirksam unterbunden.
Anwenderfreundliche Endmontage
„Wer den VOSSRing-Vormontagestutzen genauer betrachtet, stellt fest, dass er an der Stirnseite etwas länger gearbeitet ist als alle anderen Stutzen“, erläutert Berghaus. „Dieses geometrische Detail bietet bei der Endmontage höchste Leckagesicherheit und zusätzlichen Spielraum für prozesssichere Wiederholmontagen.“ Der neue Stutzen bietet nicht nur ein Höchstmaß an Sicherheit, sondern erleichtert auch die Arbeit der Monteure: Die ausgefeilte Geometrie des Werkzeugs im Rohranschlagbereich verringert den Endmontageweg von 90° auf 30°, damit wird die vom Monteur aufzubringende Arbeit um rund die Hälfte reduziert. Dieser Vorteil kommt insbesondere unter schwierigen Einbaubedingungen wie beispielsweise der Montage über Kopf, in ergonomisch ungünstigen Positionen oder bei besonders engen und kompakten Bauräumen zum Tragen.
Maximale Präzision
Der VOSSRing-Vormontagestutzen besteht aus Hochleistungsstahl, der gegenüber herkömmlichen Standardwerkzeugen nicht verschleißt und zudem noch eine 20-mal längere Werkzeugstandzeit bietet. Diese Eigenschaften machen Verschleißprüfungen komplett überflüssig: Während marktübliche Vormontagestutzen aufgrund des Aufweitens der Konuskontur regelmäßig auf ihre Funktionstauglichkeit geprüft werden müssen, gibt es diese negative Eigenschaft bei dem VOSS Werkzeug nicht. Bei Erreichen der Einsatzgrenze zerbricht der Stutzen – Montagefehler durch Werkzeugverschleiß werden auf diese Weise wirksam unterbunden.
Korrosionsschutz COSS coat-Black
Dass das neue Schneidringsystem zu 100 Prozent auf Sicherheit, Belastbarkeit und Langlebigkeit ausgelegt ist, zeigt auch die besondere Oberflächengüte des Schneidrings. „Die auf Zink und Nickel basierende Beschichtung VOSS coat-Black trotzt selbst aggressiven Medien und garantiert so auch die kundenseitig gewünschte hohe Korrosionsbeständigkeit“, veranschaulicht Berghaus. So erreicht diese Oberfläche nicht nur die höchste Korrosionsbeständigkeitsklasse K5 nach dem VDMA-Einheitsblatt 24576, sondern überschreitet die geforderten Beständigkeitswerte gegen Weiß- und Rotrost sowohl unter Laborbedingungen als auch im anspruchsvolleren Praxistest deutlich.
Fazit
Das neue Schneidringsystem gewährleistet leckage- und prozesssichere Rohrverbindungen bei höchster Druck- und dynamischer Belastbarkeit. Fehlmontagen werden durch das patentierte Anschlagkonzept sicher unterbunden. Der reduzierte Endmontageweg verringert den benötigten Kraftaufwand und erleichtert die Arbeit der Monteure – auch in engen Bauräumen. Damit ist das System besonders sicher und anwenderfreundlich.
Sichere Rohrverbindung durch Umformsystem VOSS Lok40
Sichere Rohrverbindung durch Umformsystem VOSS Lok40
Rohrverbindungen in der chemischen Industrie, der Automobil- oder Energiebranche sollen vor allem eins sein: dicht. Denn treten an diesen sensiblen Stellen Chemikalien, Gase oder Öl aus, kann das ein erhebliches Sicherheitsrisiko darstellen. Zum Verbinden von Edelstahlrohren werden in vielen Bereichen Klemmringe verwendet. Doch diese sind kostenintensiv und führen bei nicht fachgerechter Montage zu Leckagen. Das neue System VOSSLok40, das auf dem in der Hydraulik seit Jahren etablierten Prinzip der Rohrumformung basiert, stellt jetzt eine hochwertige und wirtschaftliche Alternative zum Klemmring dar. Das System punktet nicht nur mit leckagesicheren Verbindungen sondern auch mit seiner prozesssicheren Drehmomentmontage.
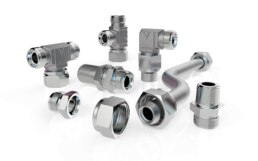
Klemmringsysteme sind in vielen Einsatzbereichen etabliert. Voraussetzung für ihre Funktionserfüllung ist allerdings, dass sie richtig angewendet und montiert werden, da sonst Leckagen drohen. Hier kommt es auf eine gute Portion Fingerspitzengefühl des Monteurs an. Mit dem neu entwickelten Umformsystem VOSSLok40 vonVOSS Fluid gibt es jetzt erstmalig eineAlternative zur 40° Klemmringverschraubung: Die Lösung gewährleistet eine wirtschaftlich optimierte und dauerhaft sichere Verbindung von Rohren mit höchster Leckagesicherheit. Da die Verschraubungskomponenten in verschiedenen Werkstoffen lieferbar sind und rein metallisch dichten, ist das System für Rohrleitungen zum Transport diverser Medien in verschiedenen Anwendungen einsetzbar: von Wasser über Öl und Gas bis hin zu korrosiven Stoffen.
Clevere Technik aus der Hydraulik
Rohrumformsysteme gelten in der Hydraulik seit Jahren als wegweisend und ersetzen zunehmend andere Verbindungsmöglichkeiten. Der Hersteller VOSS Fluid verfügt über langjährige Erfahrung mit solchen Anwendungen, und überträgt dieses Know-how mit VOSSLok40 jetzt in weitere Branchen. Wie hydraulische Formsysteme besteht auch VOSSLok40 aus drei Komponenten: einer konusförmigen Dicht- und Haltekontur, die an das Rohrende angeformt wird, einer in der Edelstahlausführung standardmäßig versilberten Mutter sowie einem Verschraubungskörper. Mutter und Verschraubungskörper sind so aufeinander abgestimmt, dass beim Anziehen der Mutter die Dichtflächen fest aufeinander gepresst werden. Auch bei hohem Druck wird eine optimale Dichtheit erreicht.
Einfache und sichere Montage
Die Konuskontur am Ende des zu verbindenden Rohres formt der Monteur mit der VOSSLok40 Umformmaschine an. Dies geschieht in drei Schritten. Zunächst wählt der Monteur über Tastendruck an der Maschine den Werkstoff des umzuformenden Rohrs aus und schiebt das Rohr bis zum Anschlag ein. Anschließend spannt die Maschine das Material und formt es um. Dabei ermittelt die Anlage automatisch die erforderliche Kraft und den optimalen Abschaltpunkt. Das schließt eine fehlerhafte Vormontage nahezu aus. Während des Umformprozesses verdrängt die Maschine das Material an der Stirnfläche von innen nach außen und glättet die Rohroberfläche am Dichtradius. Damit verbunden ist eine Entfernung kleinerer Oberflächenfehler am Rohr. Die Endmontage von VOSSLok40 erfolgt in wenigen Schritten und ist über einen Drehmomentschlüssel realisierbar. Der Montagewinkel von 120° führt zu einem deutlich kürzeren Montageweg, verglichen mit einem Winkel von 450° beim Klemmring. Dabei schützt der spürbare Kraftanstieg am Endpunkt vor einer Übermontage, die meist zu Leckagen führt. Auch häufig wechselndes oder ungeübtes Personal erreicht dadurch eine niedrige Fehlerquote und sehr gute Ergebnisse. Ein anschließendes Nachziehen der Verbindung ist jederzeit möglich.
Hohe Dichtigkeit
Selbst bei Nenndrücken bis 700 bar und Temperaturen bis –40 °C sorgt das Formsystem für eine hohe Feinstdichtigkeit. Das hat mehrere Gründe: Die massiv angeformte Kontur weist im Kontaktbereich zur Überwurfmutter eine große Anlagefläche auf, was zu einer sicheren Haltefunktion führt. Die durch Umformung erzeugte hohe Oberflächengüte verringert zusätzlich das Risiko von Leckagen. Darüber hinaus reduziert sich die Anzahl möglicher Leckagepfade um die Hälfte. Sind im Klemmringsystem durch die Außen- und Innenseite der Ringe zwei Leckagepfade vorhanden, lässt die VOSSLok40-Verschraubung nur einen einzigen zu. Dabei wird das Leckagerisiko durch die ideale Kombination von Rohrkontur und Verschraubungsstutzen als auch durch die hohe Anpresskraft der Dichtflächen auf ein Minimum gesenkt. Die überdurchschnittliche Prozesssicherheit in der maschinellen Vormontage und in der Endmontage verhindert schlussendlich Undichtigkeiten durch Anwenderfehler.
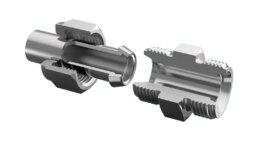
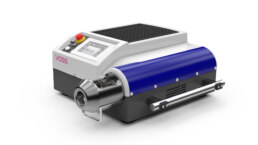
Kosteneffizientes System
Neben höchster Dichtheit und Montagefreundlichkeit profitieren Anwender von der Wirtschaftlichkeit der neuen Rohrverbindung. Kostenvorteile ergeben sich insbesondere durch die Prozesssicherheit des Systems, da Leckagen vermieden werden und die damit verbundenen Reklamationen ausbleiben. Der schnelle und automatische Umformprozess mit kurzen Taktzeiten führt zu einem optimierten Arbeitsablauf. Im Ergebnis ist VOSSLok40 damit besonders kosteneffizient und bietet neben den technischen vor allem auch wirtschaftliche Vorteile im Vergleich zu Klemmringverbindungen.
Große Bandbreite an Einsatzmöglichkeiten
Das VOSSLok40 System umfasst verschiedenste Bauformen wie Winkel, T- oder L-Verschraubungen. Die Verschraubungskomponenten sind aus Edelstahl, Stahl oder auf Kundenwunsch aus Sonderwerkstoffen gefertigt und mit unterschiedlichen Außendurchmessern erhältlich. Kombinieren lassen sich diese mit verschiedenen Rohrwerkstoffen wie beispielsweise Edelstahl 1.457, Stahl E235/E355, Aluminium oder CuNiFe-Legierungen (Kupfer-Nickel-Legierungen). Die aus Edelstahl gefertigten VOSSLok40-Komponenten sind gegenüber einer großen Bandbreite von Stoffen rundum korrosionsbeständig. Dadurch ist VOSSLok40 flexibel sehr einsetzbar. Aufgrund der besonderen Geometrie der Rohrkontur ist das System zudem kompatibel mit dem klassischen Klemmring-Stutzen. In dieser Kombination bleibt der Vorteil der Drehmomentmontage erhalten.
Fazit
Die Stärke der VOSSLok40-Verbindung besteht in ihrer hohen Dichtigkeit. Diese resultiert zum einen aus dem Zusammenspiel von Rohrkontur und Verschraubungsstutzen und zum anderen aus der Montagesicherheit des Systems: Der maschinelle Umformprozess führt zu einer sicheren Vormontage und schützt vor Fehlern. Bei der Endmontage signalisiert der spürbare Kraftanstieg den richtigen Sitz der Mutter. Da dieser Arbeitsschritt mit einem Drehmomentschlüssel erfolgen kann, wird eine Übermontage des Verbindungssystems zusätzlich verhindert. Damit leistet VOSSLok40 einen relevanten Beitrag, um enge Toleranzen einzuhalten und kostspieligen Reklamationen vorzubeugen.
Höchste Leckagesicherheit bei hydraulischen Leitungen durch Rohrumformung mit VOSSFormSQR
Höchste Leckagesicherheit bei hydraulischen Leitungen durch Rohrumformung mit VOSSFormSQR
Für die zuverlässige Verbindung von Edelstahl- und Stahlrohren auf und unter Deck bietet VOSS Fluid das Rohrumformsystem VOSSFormSQR. Mit der auch für Marine- und Offshoreanwendungen zertifizierten Lösung erzielt selbst häufig wechselndes Montagepersonal leckage- und prozesssichere Verbindungen. Das System bietet höchsten Korrosionsschutz und hält stärksten Belastungen dauerhaft stand.
Undichte Verbindungsstellen bei Schiffen oder Windparks können schnell zu großen Problemen anwachsen. Damit es erst gar nicht zu einer Leckage sowie zeit- und kostenaufwendigen Lokalisierungs- und Reparaturarbeiten kommt, hat die VOSS Fluid GmbH das Rohrumformsystem VOSSFormSQRentwickelt. Seit über zwölf Jahren ist die Lösung im Feldeinsatz – ohne dass auch nur eine einzige Leckage bekannt wurde. Der Umformprozess gestaltet sich ebenso simpel wie sicher: Im ersten Schritt erhalten handelsübliche Hydraulikrohre an einem Ende eine 24°-Rohrkontur. Die Umformung realisiert die Rohrumformmaschine VOSSForm 100 vollautomatisch. Der Bediener wählt lediglich das passende Werkzeug, schiebt das Rohr gegen die Anschlagplatte und betätigt die Starttaste. Danach formt die Maschine die VOSSFormSQR-Kontur plastisch an das Rohr an. Zum Abschluss der Vormontage wird das umgeformte Rohrende mit einer zusätzlichen Weichdichtung versehen. Dann folgt die Endmontage: Der Monteur setzt mit der Stirnseite des bearbeiteten Rohres auf dem Grund des Verschraubungsstutzens auf. Dies sorgt für einen stabilen Sitz und sicheren Anschlag.
Anschließend zieht er die Mutter an. Da es sich um eine speziell von VOSS Fluid entwickelte SQR-Funktionsmutter mit integriertem Klemmring handelt, wird das Rohr während der Endmontage automatisch radial fest eingespannt. So entsteht eine besonders sichere und hochwertige Verbindung. Der spürbare Kraftanstieg beim Anziehen der Mutter signalisiert dem Monteur zuverlässig das Montageende. Unter- oder Übermontagen sind auf diese Weise praktisch ausgeschlossen. Ein weiterer wichtiger Vorteil: Im Vergleich zu marktüblichen Systemen verringert sich der Montageweg mit dem Rohrumformsystem von VOSS Fluid deutlich. Es werden nahezu identische Ergebnisse wie bei vergleichbaren Dichtkegelverschraubungen erzielt. Dies reduziert den benötigten Kraftaufwand sowie die Montagezeit und kommt vor allem unter schwierigen Einbaubedingungen wie beispielsweise der Montage über Kopf, in ergonomisch ungünstigen Positionen oder bei besonders engen und kompakten Bauräumen zum Tragen.
Höchste Dichtheit und Belastbarkeit
VOSSFormSQR Rohrverschraubungen bieten selbst im Feinbereich eine vollständig dichte Verbindung. Dies ist eine der wichtigsten Voraussetzungen für den Einsatz auf hoher See. Die hohe Dichtheit ist unter anderem auf die zusätzliche Weichdichtung zurückzuführen, die gegenüber einer rein metallischen Abdichtung deutliche Vorteile bietet. Sie verhindert wirksam das Schwitzen der Verbindung – und dies für überdurchschnittlich lange Zeit. Denn das enge Anliegen des Rohres im Stutzengrund, die sogenannte metallische Primärdrosselung, bewirkt eine Dämpfung der Druckwechselbeanspruchung. Dieses marktweit einzigartige Konzept beugt dem Walken oder Ausspülen der Weichdichtung vor und garantiert somit langfristig dichte Verbindungen. Das Rohrverschraubungssystem erfüllt darüber hinaus höchste Ansprüche an Belastbarkeit und Sicherheit. Schließlich müssen Marine- und Offshoreanwendungen aufgrund der stetigen Vibrationen eine besonders hohe Biegewechselfestigkeit aufweisen. Bei VOSSFormSQR sorgen der in der Überwurfmutter befindliche Klemmring und eine tiefe Rohreinspannung für die zuverlässige Resistenz gegen hohe Biegewechselbelastungen: Zum einen wird ein überdurchschnittlich langer Teil des Rohres durch den Verschraubungsstutzen abgestützt.
Zum anderen spannt der Klemmring das Rohr radial am Umfang ein und nimmt dadurch dynamische Belastungen bereits vor dem kritischen Bereich auf. Dies verhindert einen potenziellen Bruch durch Kerbwirkung und erhöht die Druckbelastbarkeit und Bruchsicherheit enorm. Aufgrund der hohen Qualität hält VOSS Fluid die Zulassungen aller Schiffbauklassen der International Association of Classification Societies (IACS). Unter der Dachorganisation IACS sind international anerkannte Klassifikationsgesellschaften zusammengeschlossen, die anwendungsspezifische Anforderungen und Prüfverfahren festlegen und so die internationalen Qualitätsstandards definieren.
Langzeitkorrosionsschutz
Dass VOSSFormSQR zu 100 Prozent auf Sicherheit, Belastbarkeit und Langlebigkeit ausgelegt ist, zeigt auch die besondere Oberflächengüte der Rohrverbindungskomponenten. Die auf Zink und Nickel basierende Beschichtung VOSS coat trotzt selbst aggressiven Medien und garantiert eine besonders hohe Korrosionsbeständigkeit. So erreicht die Oberfläche nicht nur die höchste Korrosionsbeständigkeitsklasse K5 nach dem VDMA-Einheitsblatt 24576, sondern überschreitet die geforderten Beständigkeitswerte gegen Weiß- und Rotrost sowohl unter Laborbedingungen als auch im anspruchsvolleren Praxistest deutlich. Für einige Marine- und Offshoreanwendungen bedeutet dies: Der Oberflächenschutz VOSS coat ist so wirkungsvoll, dass Stahlverrohrungen mit VOSS FluidRohrverschraubungen entgegen der gängigen Praxis teilweise gar nicht mehr überlackiert werden müssen.
Für Anwendungen in Edelstahl kommt das Rohrumformsystem VOSSFormSQRVA zum Einsatz. Alle Verschraubungskomponenten sind in diesem Fall aus Edelstahl gefertigt und weisen komplett identische Produkteigenschaften und Vorteile auf. Höchste Prozess- und Leckagesicherheit, größte Resistenz gegen Belastungen und ausgezeichnete Korrosionsbeständigkeit – diese Merkmale machen das Rohrumformsystem von VOSS Fluid zur optimalen Lösung für die Schiffbau- und die Offshoreindustrie.
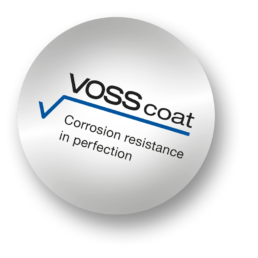
Die Unterschätzte Notwendigkeit
Die unterschätzte Notwendigkeit
Rohrverbindungskomponenten sind ein entscheidender Bestandteil von Hydrauliksystemen. Funktionalität und Langlebigkeit hängen unmittelbar von ihnen ab. Unterschätzt wird jedoch die Bedeutung und Auswahl eines hochwertigen Korrosionsschutzes – und das kann Folgen haben.
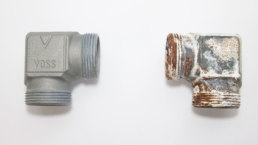
Wechselnde Temperaturbedingungen und schlagartig auftretende Druckspitzen: Hydrauliksysteme sind höchsten Belastungen ausgesetzt. Unabhängig vom konkreten Einsatzzweck oder von der Abdichtungs- und Belastungsart kommt der Oberflächenbeschichtung von Rohrverbindungskomponenten eine besondere Bedeutung zu. Sie ist Voraussetzung für einen dauerhaften Korrosionsschutz und damit für funktionsbeständige Bauteile. Die Beschichtung dieser Bauteile ist jedoch ein aufwendiger Prozess, bestehend aus einer Vorbehandlung mit Entfetten, Beizen und Dekapieren, der eigentlichen Beschichtung mit einer individuellen Nachbehandlung bis hin zum Passivieren und Auftragen der abschließenden Versiegelung. Um vermeintlich Kosten zu sparen wird auf Hersteller- wie auch auf Kundenseite daher häufig nach der günstigsten Lösung oder entsprechenden Alternativen gesucht. Das kann jedoch ins Auge gehen, vor allem dann, wenn aus einem vermeintlich günstigen Angebot plötzlich billiger Schrott wird. Denn mit einem können die Verwender eines minderwertigen Korrosionsschutzes nicht rechnen: Langlebigkeit. Wer sich aber nicht dauerhaft auf die Funktionsfähigkeit der Bauteile in hydraulischen Systemen verlassen kann, für den wird der Sparzwang schnell zur Milchmädchenrechnung.
Sparen an der falschen Stelle
Vor dieser Einstellung darf also gewarnt werden, denn hier wird an der falschen Stelle gespart. Beispielsweise fällt die Wahl häufig auf eine herkömmliche Zinkbeschichtung. Ein Unternehmen, das auf Qualität setzt, langfristig rechnet und auf eine hohe Prozesssicherheit Wert legt, geht in diesem Bereich keine Kompromisse ein. Der Wipperfürther Hersteller von Rohr- und Schlauchverbindungskomponenten VOSS Fluid setzt bei seinem Korrosionsschutz auf eine Eigenentwicklung auf Basis einer Zink-Nickel-Beschichtung namens VOSS coat. Diese Beschichtung hält selbst aggressiven Medien, wie beispielsweise verschiedensten Düngemitteln, langfristiger stand. Kommen freiliegende Teile beispielsweise in Kontakt mit Mineral- oder Nitratdüngern, kann dies zu verstärkter Korrosion führen. Daher werden sämtliche VOSS-Produkte mit dieser Legierung ausgestattet. Nach der erfolgreichen Markteinführung im Jahr 2007 hat VOSS seinen Korrosionsschutz stetig weiterentwickelt. Die Schichtdicke liegt zwischen 6 bis 15 μm. Bis zu 16 % beträgt der Nickelanteil in der VOSS coat-Oberfläche. Auf eine Basisschicht folgt eine zusätzliche Passivierung und als Finish eine Versiegelung. Unternehmen, die durchgängig auf VOSS Rohrverbindungskomponenten setzen, profitieren daher von einem ausnahmslos hohen Korrosionsschutz. Zudem bildet sich, anders als bei reinen Zinkoberflächen, kein Rot- oder Weißrost.
Zink-Nickel ist nicht gleich Zink-Nickel
Die Besonderheit beim Korrosionsschutz von VOSS ist die Art und Weise, wie das Wipperfürther Unternehmen die hohe Qualität seiner schützenden Beschichtung sicherstellt: mit einer eigens dafür erbauten Galvanik. Statt auf externe Dienstleister zu setzen, beschloss VOSS frühzeitig, in eine eigene Gestell- und Trommelanlage zu investieren. So hat VOSS die Qualitätssicherung und Weiterentwicklung seines Korrosionsschutzes in der eigenen Hand und ist nicht auf Dritte angewiesen, wie Frank Müller, Werksleiter bei VOSS, unterstreicht: „Mit unserer eigenen Galvanik haben wir die Möglichkeit, den Prozess exakt auf jedes Bauteil abzustimmen und je nach Kundenwunsch flexibel zu reagieren. Hier haben wir alles selbst unter Kontrolle, und unsere Kunden wissen, dass sie die Qualität aus einer Hand erhalten.“ In Praxistests, u.a. mit Flüssigdüngermitteln, hat sich die VOSS-eigene Zink-Nickel-Beschichtung bereits mehrfach bewährt, sodass auch sechs Monate nach Testbeginn nur marginale Spuren von Korrosion zu erkennen waren. Damit schneidet VOSS coat im direkten Vergleich mit anderen Zink-Nickel-Oberflächen am besten ab – ein Hinweis darauf, dass die hohe Korrosionsbeständigkeit nicht allein auf die Art der Beschichtung zurückzuführen ist. Für VOSS war dies ein weiteres Argument dafür, in die eigene Galvanik zu investieren.
VOSS beschichtet in eigener Galvanik
Diese Galvanik wurde 2009 im Werk Wipperfürth auf einer Grundfläche von 2.500 m2 errichtet. Diese Investition zahlte sich aus, da die eigens entwickelte Beschichtung VOSS coat für viele Kunden zum wesentlichen Argument wurde, langfristig auf VOSS-Komponenten zu vertrauen. Aufgrund der stetig steigenden Nachfrage nach VOSS-Produkten wurde die Kapazität der Galvanik in diesem Jahr weiter ausgebaut. Die gesamte Anlage ist zweigeschossig errichtet, sodass die Mitarbeiter getrennt von der Chemie arbeiten können – eine Bauweise, die in anderen Galvaniken selten vorzufinden ist. In der unteren Etage, dort wo auch die Gestell- und Trommelanlage bestückt werden, geschehen die komplette Kontrolle und die Prozessmanagement. Auf Monitoren kann das Personal in Echtzeit verfolgen, wo sich welcher Warenträger gerade befindet und wie lange der einzelne Prozessschritt noch dauert. Darüber hinaus können die einzelnen Badparameter, wie beispielsweise die Temperatur, der pH-Wert sowie die Stromparameter, exakt eingesehen und überprüft werden. Die zu galvanisierenden Teile kommen aus der mechanischen Fertigung, in der die Oberflächen innen und außen größtenteils zerspanend bearbeitet werden. Die Komponenten werden in der Gestellanlage sortiert nach Größe und Bauweise einzeln per Hand auf die Gestelle gesteckt.
Rohrverschraubungen, die aufgrund ihrer Größe, ihres Gewichts oder ihrer äußeren Geometrie weniger beschädigungsanfällig sind, kommen in die Trommelanlage. Nach der Bestückung der Gestelle beziehungsweise der Trommeln fahren die Warenträger in die obere Etage, um dort die verschiedenen Galvanikbäder zu durchlaufen, in denen die Komponenten die VOSS coat-Beschichtung erhalten.
Zink und Nickel, die mit einem nahezu hundertprozentigen Reinheitsgehalt als Metall in den Elektrolyt (Lösung von Salzen / Metallsalzen) eingehängt werden, wirken als Anode (Pluspol). Die ebenfalls im Bad befindliche Ware wirkt wie eine Katode (Minuspol). Durch das galvanische Prinzip wandern die Metallionen zum Werkstück und lagern sich darauf ab. Im Obergeschoss geschieht der gesamte Prozessdurchlauf der befüllten Gestelle bzw. Trommeln getrennt voneinander in zwei separaten Anlagen. Über Transportwagen werden die einzelnen Chargen automatisch zu den vom jeweiligen Prozessschritt abhängigen Bädern transportiert und dort eingetaucht.
Labor und Versuchsgalvanik sichern hohe Qualität
Für die richtigen Prozessparameter und die chemische Zusammensetzung der Bäder sorgt das unternehmenseigene Labor, in dem VOSS die Beschichtung permanent überwacht und zudem weiterentwickelt. Zu diesen Optimierungszwecken leistet sich VOSS sogar eine eigene Versuchsgalvanik – eine exakte Kopie der Originalanlage in Miniaturform, bei der alle Prozessschritte nachgestellt und Verbesserungen vor dem Einfließen in die Großserie geprüft werden. Zur Überwachung der Qualität und der gewünschten Funktionsfähigkeit von Weiterentwicklungen gehören auch Salzsprühnebeltests, welche in der hauseigenen Sprühkammer durchgeführt werden. Die beschichteten Bauteile werden dabei unter standardisierten Bedingungen einem Salzsprühnebel ausgesetzt, um deren Korrosionsbeständigkeit nachzuweisen. Neben den Qualitätskontrollen werden im Labor auch permanent Messungen des Abwassers vorgenommen und streng überwacht. Im Zuge des Ausbaus wurde in der oberen Etage eine moderne Zu- und Abluftanlage inklusive Luftwäscher erweitert. Die benötigte Prozesswärme wir durch ein Blockheizkraftwerk im Nebengebäude zur Verfügung gestellt.
Für die nun durchgeführte umfangreiche Kapazitätserweiterung der Galvanik plante VOSS Fluid sehr vorausschauend, da die komplette Ausbaustufe bereits in der eigentlichen Anlagenplanung im Jahr 2008 berücksichtigt wurde. Unter anderem wurden bereits damals die nun benötigten Flächen für die zusätzlichen Bäder an den entsprechenden Stellen freigehalten.
Fazit: Qualität zahlt sich aus
In Korrosionsschutz zu investieren lohnt sich – einerseits für die Kunden (Langlebigkeit) – andererseits für die Hersteller, die wie VOSS Premiumqualität liefern wollen. VOSS coat sticht unter den hochwertigeren Beschichtungen auf Zink-Nickel-Basis noch einmal heraus, da sie einen bis zu 10-mal stärkeren bzw. längeren Schutz als herkömmliche Zinkbeschichtungen liefert. Aufgrund der stetigen Weiterentwicklung erreicht VOSS coat mittlerweile mehr als 2.000 Stunden Korrosionsbeständigkeit – ein stichhaltiges Kriterium für viele Kunden, denn damit übertreffen die Wipperfürther Experten die höchste Korrosionsschutzklasse K5 des VDMA-Einheitsblattes 24576, in dem eine Rotrostbeständigkeit der Oberfläche von mindestens 720 Stunden gefordert wird. VOSS-Rohrverbindungen sind also auch unter realen Bedingungen dauerhaft funktionsfähig und gleichzeitig eine wirtschaftliche Alternative zu Edelstahl. Der Kunde profitiert dadurch von einer deutlich höheren Prozesssicherheit.
Unübertroffen schnell und prozesssicher
Unübertroffen schnell und prozesssicher
In vielen Werkstätten ist es bereits der neue Shootingstar: Das VOSS Vormontagegerät Typ 90 Comfort revolutioniert zurzeit den Markt für die Serienproduktion von Rohrleitungen mit DIN-Verschraubungen. Ein Höchstmaß an Prozesssicherheit in der Schneidringvormontage sowie um bis zu 60 % verkürzte Taktzeiten sind nur zwei der überzeugenden Ergebnisse des Geräteeinsatzes.
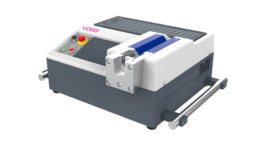
Rund um den Globus werden tagtäglich unzählige Kilometer an Rohrleitungen gefertigt, die in unterschiedlichsten Systemen der Stationär- und Mobilhydraulik Einsatz finden. Ihnen gemein ist die Forderung nach sicheren und wirtschaftlichen Rohrverbindungskomponenten. Die Wahl fällt oftmals auf Schneidringsysteme, die – einen Qualitätshersteller vorausgesetzt – bei mustergültiger Montage hohe Leckagesicherheit bieten. Für die korrekte Vormontage sind am Markt diverse Hilfsmittel erhältlich – von Handvormontagestutzen für die Einzelmontage im Schraubstock über Servicemaschinen für die Baustelle bis hin zu Vormontagegeräten für die Serienfertigung. Bei den meisten Montagearten ist der jeweilige Monteur für die korrekte Einstellung und Handhabung zuständig. Genau dieser Sachverhalt birgt allerdings Fehlerpotenzial. Schneidringe können falsch herum aufgesetzt werden. Auch könnten unpassende Schneidringe ausgewählt werden.
Nicht immer werden fehlerhaft vormontierte Leitungen erkannt und ausgemustert; das gilt insbesondere bei häufig wechselndem oder unerfahrenem Personal. Die Folge: Leckagen an Maschinen und Anlagen, die durch Servicetechniker mit teilweise hohem Kosteneinsatz behoben werden müssen – vom Imageschaden ganz zu schweigen. Auch wenn es sich dabei um Ausnahmefälle handelt und qualitativ hochwertige Schneidringsysteme ein sehr hohes Maß an Leckagefreiheit bieten – mit diesem Status quo wollte sich der Verbindungstechnikspezialist VOSS Fluid nicht zufriedengeben. Daher brachte das Unternehmen ein neues Vormontagegerät für die Serienmontage von Schneidringen auf Stahl- und Edelstahlrohre auf den Markt: das Typ 90 Comfort. Die Maschine bietet höchste Prozesssicherheit bei unübertroffen schnellen Taktzeiten.
Fehlmontage ade!
Das massive Plus an Sicherheit bietet das neue Vormontagegerät durch die Kombination von automatisierten Bedien- und Handlingprozessen sowie zuverlässiger Fehlererkennung. Der Monteur rüstet das Vormontagegerät lediglich mit dem zu verarbeitenden Rohr sowie dem passenden, verschleißfest gefertigten VOSS Werkzeug und startet den Vormontageprozess. Ab diesem Zeitpunkt realisiert der Typ 90 Comfort alle weiteren Aufgaben selbsttätig. Zum Einsatz kommt modernste Technik, die zur automatischen Identifizierung von Objekten eingesetzt wird: Im Kolben des Vormontagegeräts befindet sich ein RFID-Lesegerät, zudem sind alle Werkzeuge mit einem RFID-Chip ausgestattet. Sobald die Maschine gerüstet wird, liest sie den Werkzeugchip aus und stellt den benötigten Arbeitsdruck ein. Direkt im Anschluss startet die druck-und wegabhängige Vormontage. So erzielt jeder Monteur mit Leichtigkeit ein präzises und stets reproduzierbares Ergebnis. Durch die hohe Automatisierung sind Bedienfehler selbst bei ständigen Werkzeugwechseln wirksam unterbunden. Allenfalls ein unkorrektes Rüsten der Maschine wäre noch denkbar. In diesen Fällen greift jedoch sofort die integrierte Fehlererkennung: Das Vormontagegerät erkennt zuverlässig alle denkbaren Mängel – beispielsweise einen falsch positionierten oder fehlenden Schneidring – und zeigt sie umgehend auf dem Display an. Ein versehentliches Übersehen der Warnung ist ausgeschlossen. Der Monteur muss die Information manuell bestätigen, um den Fertigungsprozess fortsetzen zu können. Das Ergebnis ist ein Maximum an Prozesssicherheit in der seriellen Schneidringvormontage.
Blitzschnell und hochflexibel
Herausragende Ergebnisse liefert das VOSS-Vormontagegerät jedoch nicht allein im Hinblick auf die Prozesssicherheit. Die Wirtschaftlichkeit des Systemeinsatzes zeigt sich auch in den extrem kurzen Taktzeiten: Bei kleineren Durchmessern liegt die Geschwindigkeit je Schneidringmontage bei ca. 1,8 Sek., beim größten Rohraußendurchmesser von 42 mm bei ca. 2,5 Sek. Im Vergleich zum Vorgängermodell reduzieren VOSS Fluid Kunden ihre Taktzeiten durchschnittlich sogar um über 60 %. Darüber hinaus bietet das Vormontagegerät maximale Flexibilität in der Fertigung. Das durchdachte Maschinendesign erlaubt die problemlose Verarbeitung unterschiedlichster Rohrgeometrien. Auch enge 180°-Bögen und besonders sperrige Leitungsverläufe lassen sich qualitativ hochwertig vormontieren. Möglich macht dies die V-förmige Aussparung am Doppelkolben des Geräts. Bei Bedarf kann der Typ 90 Comfort mithilfe eines Maschinenumbaus durch VOSS Fluid auch für die Vormontage von BV-10 Bördelkegeln und ZAKO Kragenringen eingesetzt werden. Auch bei diesen Rohrverbindungskomponenten gewährleistet das Gerät höchste Prozesssicherheit. Durch die konstante, wegabhängige Montage gehören beispielsweise übermontierte Kegel der Vergangenheit an.
Maßgeschneiderte Systemeinstellung
Jedes Unternehmen, das sich für das neue Vormontagegerät entscheidet, erhält eine komplett auf die individuellen Anforderungen zugeschnittene Maschine. Das betrifft die Anzahl und Zuordnung der verschleißfest gefertigten Werkzeuge ebenso wie optionale Zusatzausstattungen wie Fußschalter oder eine Bedienung für Linkshänder. Die kundenindividuelle Parametrisierung und Kalibrierung der Maschine übernimmt ein VOSS Servicetechniker direkt vor Ort. Anhand von Musterstücken wird bei Bedarf für jedes Rohrmaterial und jeden Durchmesser eine separate Programmierung vorgenommen und Codewort-geschützt gespeichert. Ein USB-Anschluss bietet die Möglichkeit der externen Speicherung und Archivierung, außerdem kann die Programmierung auf diese Weise problemlos auf weitere Geräte überspielt werden. Nachträgliche Anpassungen für Sonderanwendungen sind ebenfalls mühelos umsetzbar. Die frei programmierbare Zähleinrichtung bietet dem Werkstattmeister zudem die Möglichkeit zur statistischen Auswertung; auch Datum und Uhrzeit einer Fehlermeldung sind nachvollziehbar.
Fazit
Das neue Vormontagegerät eignet sich somit vor allem für Unternehmen, die großen Wert auf eine prozesssichere, zügige und wirtschaftliche Vormontage von Schneidringen legen oder häufig Rohre mit engen Radien verarbeiten. Zusammengefasst erzielt das Typ 90 Comfort von VOSS Fluid folgende Ergebnisse:
- ein Höchstmaß an Prozesssicherheit in der Schneidringvormontage
- extrem schnelle Taktzeiten über alle Rohrgrößen
- präzise, reproduzierbare Montageergebnisse
- selbstständige Verhinderung von Fehlmontagen
- Montagen auch bei engsten Rohrbögen
- hohe Werkzeugstandzeiten
Sichere und effiziente Schlauchverbindungen
Sichere und effiziente Schlauchverbindungen
Ein prozesssicheres und effizientes Hydrauliksystem ist angesichts der stetig steigenden Anforderungen am Markt eine zentrale Herausforderung. Für einen zuverlässigen und langlebigen Maschineneinsatz kommt es daher auf die richtige Auswahl und ein perfektes Zusammenspiel aller Einzelkomponenten an. Mit der Erweiterung des Produktportfolios um Schlaucharmaturen bietet VOSS Fluid nun eine anforderungsgerechte Verbindungstechnik für das gesamte Leitungssystem an.
VOSS Fluid, Qualitätshersteller für Rohrverschraubungstechnik, hat sein Produktspektrum sinnvoll erweitert: Neben moderner Rohrverbindungstechnik liefert das Unternehmen nun auch sämtliche Komponenten für den Schlauchanschluss mobiler und stationärer Maschinen und Anlagen. Im Ergebnis reduzieren Anwender die Anzahl ihrer Lieferanten und erhalten darüber hinaus eine einheitliche Produktqualität auf höchstem technischem Niveau, die vor allem in Hinblick auf die Leckagesicherheit und Korrosionsbeständigkeit überzeugt. Hydraulikkomponenten aus dem Hause VOSS Fluid stehen für moderne hydraulische Verbindungstechnik aus einer Hand.
Wegbereiter für korrosionsbeständige Schlaucharmaturen
Ausschlaggebend für den flächendeckend erfolgreichen Einsatz sind ein herausragender Produktstandard, die hohe Beratungskompetenz sowie anwendungsgerechte Lösungen.
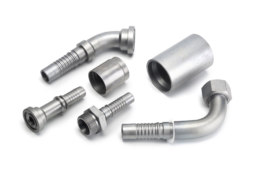
Das Sortiment an Schlaucharmaturen verfügt ebenfalls wie das gesamte Produktprogramm über die typische VOSS Zink-Nickel-Oberflächenbeschichtung. Um das hohen Qualitätsniveau dauerhaft zu halten, werden die Produkte wiederkehrend allen notwendigen Prüfungen unterzogen. Dazu gehören das hydrostatische Prüfverfahren nach EN ISO 1402 und die Druck-Impulsprüfung nach EN ISO 6803. Darüber hinaus ist die Validierungsprüfung wichtiger Bestandteil der umfassenden Serviceleistung von VOSS Fluid: Neben den gängigen Pressmaßtabellen, welche die erforderlichen Pressmaße für die Herstellung von Schlauchleitungen liefern, testet das Unternehmen individuell die vom Kunden verwendeten Schläuche verschiedenster Hersteller in Form einer sogenannten „Freiprüfung“. Durch Fertigungstoleranzen sind diese ständigen Veränderungen ausgesetzt. Daher stellt VOSS in regelmäßigen Abständen die korrekten Werte bereit und garantiert, dass die Verbindungskomponenten den Arbeitsdrücken sämtlicher Schläuche sicher standhalten. Alle Produktprüfungen können durch das eigene Prüflabor Inhouse durchgeführt werden. Aussagekräftige Daten über die Produktsicherheit fließen auf diese Weise direkt an den Kunden, der von einer umfassenden technischen Beratung und Funktionssicherheit profitiert.
Erhöhte Langlebigkeit
Was bei Rohrverbindungskomponenten maßgeblich im Vordergrund steht, ist für Schlaucharmaturen ebenfalls Standard: Eine dauerhafte Korrosionsbeständigkeit mithilfe der bewährten VOSS Zink-Nickel-Oberfläche. Durch diese Oberflächenbeschichtung wird die Funktionsfähigkeit des Bauteils um ein Vielfaches verlängert. Prüfergebnisse aus der Salzsprühnebelkammer haben ergeben, dass die Oberfläche eine vielfach höhere Beständigkeit gegenüber Rotrost aufweist als reine Verzinkungen. Mit den Zink-Nickel-beschichteten Schlaucharmaturen und Verbindungskomponenten treffen Kunden eine nachhaltige Produktentscheidung, da Bauteile dadurch langfristig wirtschaftlich im Einsatz sind und auch optisch nicht als „Qualitätsmangel“ durch den Endanwender wahrgenommen werden.
Die drei Hauptanforderungen an Schlauchleitungen
Höchstleistungen in der Hydraulik erfordern höchste Lösungskompetenz. Hydraulikschläuche bestehen aus Elastomeren, die dem Druckmedium im Innern über lange Zeit standhalten müssen. Um die Prozesssicherheit zu gewährleisten, spielen die drei Einflussfaktoren Druck, Temperatur und das eingesetzte Medium eine besondere Rolle für die hydraulische Auslegung der Maschine. Im ersten Schritt ist zu beachten, ob besondere Einbausituationen wie beispielsweise Reduzierungen oder Befestigungspunkte, die der Funktionalität der Maschinen zugutekommen, die Druckleistung behindern. Im zweiten Schritt muss der Temperaturbereich unter die Lupe genommen werden: Zu hohe Betriebstemperaturen können sich negativ auf die Bauteile auswirken.
Druck
Temperatur
eingesetztes Medium
Durch Oxidation bilden die Druckmedien schon nach relativ kurzer Einsatzdauer Säuren, welche die elastomeren Bestandteile des Systems sowie die Buntmetalle angreifen können. Zudem schleicht sich in temperaturlastigen Systemen durch Kondensation immer ein für die Anwendung nicht gern gesehener Gast ein: Wasser. Ungelöstes Wasser im Öl setzt sich in der gequollenen Innenschicht der Schlauchleitung ab. Durch ungünstige Temperatur-Druck-Verläufe besteht die Möglichkeit, dass die Wassereinlagerung verdampft. Kleine Teile des umliegenden Elastomers sprengen dabei heraus und beschädigen die Schlauchleitung im Innern. Bei diesem Phänomen spricht man von dem sogenannten Popcorning-Effekt. Der dritte Punkt bezieht sich auf das eingesetzte Medium. Die sich heute im Einsatz befindlichen Fluide reichen von Wasser-Öl-Emulsionen über Standard- und Sondermineralöle bis hin zu biologisch abbaubaren Hydraulikflüssigkeiten auf pflanzlicher, mineralischer und synthetischer Basis. Als eine Folge des Zusammenspiels von Elastomer und Fluid tritt das Quellen des Gummiwerkstoffes auf.
Nimmt dieser das eingesetzte Fluid in sich auf, vergrößert sich sein Volumen in einem unerwünschten Maße, sodass in den Innenschichten von Schlauchleitungen Schäden entstehen können und sich die Leitungsdurchmesser verengen. Um diesen unerwünschten Effekten entgegenzuwirken, ist eine durchdachte Systemauslegung und -auswahl notwendig.
Denn verengte Leitungsdurchmesser werden nicht nur durch Quellen des Hydraulikschlauches hervorgerufen. Die erste Querschnittsverengung kommt bereits durch den Schlauchnippel zustande. Weitere Verengungen können beispielsweise durch einfallende 90° gebogene Schlaucharmaturen auftreten. Diese weisen innerhalb der Biegung eine hohe Ovalität auf, wodurch Verwirbelungen und Druckverluste entstehen. Unter Einbeziehung aller notwendigen Parameter bei der Auslegung der Hydraulikanlagen werden Ausfälle und Schäden weitestgehend vermieden. Von Vorneherein wird die Frage gestellt, was die Schlauchleitung im Einsatz leisten muss: Für hochdynamische Beanspruchungen bietet VOSS ein Design für Schlaucharmaturen mit Ausreißsicherung. Diese werden durch ein spezielles Verpressverfahren mit dem Schlauch verbunden, so dass sich kein Elastomer mehr zwischen Armatur und Schlauch befindet. Von außen und innen besteht dadurch ein direkter Kontakt mit dem Stahl, wodurch der daraus resultierende Formschluss zwischen Fassung, Schlauch und Armatur das Herauswandern des Schlauches verhindert. Auch bei Druckstufenerhöhungen der Armatur werden Leckagen auf diese Weise weitestgehend vermieden.
Fazit
Mit seinem Portfolio an aufeinander abgestimmter Rohr- und Schlauchverbindungstechnik ermöglicht VOSS Fluid eine gleichbleibend hohe Qualität. Die individuellen Anforderungen für den Anschluss Rohr-zu-Schlauch immer im Blick, erhalten Kunden vielfältige Hydraulikkomponenten, die auf Druck, Temperatur und Fluid optimal angepasst sind und so eine hohe Effizienz und Langlebigkeit im Betrieb erzielen.
Sichere Hydraulik dank hochwertiger Verbindungstechnik
Sichere Hydraulik dank hochwertiger Verbindungstechnik
Hohe Wirkungsgrade, wechselnde Temperaturbedingungen und häufige Lastwechsel – Hydrauliksysteme stationärer und mobiler Arbeitsmaschinen sind stetigen Belastungen ausgesetzt. Um langfristig die größtmögliche Funktionsfähigkeit zu gewährleisten, ist eine korrosionsbeständige und präzise Verbindungstechnik unerlässlich.
Kleine Komponenten mit großer Systemfunktion: Die Prozesssicherheit hydraulischer Verbindungstechnik ist branchenübergreifend ausschlaggebend für den zuverlässigen und wirtschaftlichen Betrieb von modernen Arbeitsmaschinen. Ein zentraler Aspekt ist dabei das Streben nach mehr Energieeffizienz – doch mit den Wirkungsgraden nehmen auch die Belastungen in der Fluidtechnik zu. Damit permanent beanspruchte Anlagen wie Kunststoffspritzgießmaschinen und Großbagger im Bergbau auch unter härteren Bedingungen zuverlässig funktionieren, sind Komponenten entsprechend der Anforderung an die Leckagesicherheit der Verbindungsstelle und mit einem beständigen Korrosionsschutz notwendig. Für den Anwender bedeutet das: Neben der Auswahl systemgerechter Verbindungskomponenten stehen eine fachgerechte Montage sowie die Wahl eines kompetenten Zulieferers im Mittelpunkt.
Die VOSS Fluid GmbH ist Hersteller von Rohrverbindungssystemen und Systempartner des internationalen Maschinenbaus. Das Produktportfolio umfasst Rohrverbindungen für die Stationär- und Mobilhydraulik, darunter Schneidring- und Bördelverschraubungen, Rohrumformsysteme, Flanschverbindungen, Ventile und Zubehör. VOSS Fluid verfügt über langjährige Kompetenz in der Fertigung von Verbindungsteilen gemäß den Anforderungen der Kunden und setzt diese in der Entwicklung der Systemlösungen und der technischen Beratung ihrer Kunden gezielt ein. Das Ergebnis sind gleichbleibend hochwertige Bauteile, ein hoher Korrosionsschutz sowie eine fachgerechte, zeiteffiziente Montierbarkeit der Komponenten und langzeitdichte Hydrauliksysteme.
"Oberflächliche" Qualität mit fachlicher Tiefe
Eine zentrale, qualitative Bedingung ist die Beschichtung der Rohrverbindungen. Sie ist Voraussetzung für einen dauerhaften Korrosionsschutz sowie funktionsbeständige und damit wirtschaftliche Bauteile: VOSS Fluid setzt hierbei für alle Rohrverschraubungen die hauseigene, nachhaltige Zink-Nickel-Beschichtung VOSS coat ein. Diese erfüllt sämtliche Vorgaben der EU-Altauto-Richtlinie, die seit 2007 Chrom-VI-haltige Oberflächen untersagt. Gemeinsam mit unabhängigen Forschungsinstituten und Universitäten, wie der Fachhochschule Aalen, wurde ein Korrosionsschutz entwickelt, der im Vergleich der Basisschichten etwa um ein Zehnfaches besser ist als konventionell eingesetzte Zinkschichten. Anders als reine Zinkoberflächen bildet Zink-Nickel keinen ausgeprägten Weißrost bei der Korrosion, sondern erzeugt lediglich einen leichten Grauschleier.
Die in der EG-Verordnung 1907/2006 aufgeführten Grenzwerte zur Bestimmung der Nickellässigkeit von Produkten, die in direkten und länger andauernden Kontakt mit der Haut kommen, werden um das 50-Fache unterschritten. Im direkten Vergleich der VOSS coat Oberfläche mit einer 2-Euro-Münze wird dieser Grenzwert sogar um das 2.230-Fache unterschritten. Die Oberfläche ist durch den harten Nickelanteil nicht nur umweltverträglich, sondern auch verschleißfester gegenüber mechanischen Belastungen, denen Hydraulikverschraubungen vom Transport über die Montage bis zum Einsatz ausgesetzt sind.
VOSS coat besteht aus einer Zink-Nickel-Basisschicht, die anschließend passiviert und abschließend versiegelt wird. Diese drei Schichten verhindern die Korrosion des Grundwerkstoffs und werten die Verbindungskomponenten nachhaltig auf. Nach dem VDMA-Einheitsblatt 24576 erreicht die Zink-Nickel-Oberfläche die höchste Korrosionsbeständigkeitsklasse K5. Diese bezeichnet die Schutzleistung der Oberfläche, die eine Beständigkeit von mindestens 720 Stunden gegen Rotrost und mindestens 360 Stunden gegen Weißrost nachweist.
Unter Laborbedingungen mit unmontierten Teilen wurde im Salzsprühnebeltest nach DIN EN ISO 9227 sogar eine Korrosionsbeständigkeit von mehr als 2.000 Stunden erreicht. Im Praxistest mit Zufallsware aus der laufenden Produktion wurde nach deren Handling und Montage bewiesen, dass auch bei 1.000 Stunden keine Grundmetallkorrosion auftritt.
Für optimale Montagedrehmomente werden die Reibbeiwerte in der Entwicklung und Produktion für Schneidringverschraubungen laufend verbessert: Dadurch sind diese deutlich geringer als bei anderen Zink-Nickel-Beschichtungen. Je nach Verbindungsbauteil werden ein Gleitmittel und eine partielle Innenbeschichtung eingesetzt, beispielsweise bei Überwurfmuttern. Montagesichere Produktionsprozesse beim Kunden unterstützen erfahrene Anwendungstechniker, welche die Monteure und Instandhalter begleiten – von der Auswahl der systemgerechten Hydraulikverschraubung über Schulungen rund um leckagefreie Verbindungen bis zu regelmäßigen Montageaudits.
Know-how-Vorsprung: In-house-Galvanik
Grundlegende Voraussetzung für die qualitativ hochwertige Beschichtung der Rohrverbindungen ist die werkseigene Galvanik, die einem hohen technologischen Standard sowie den aktuellen Umweltbestimmungen für Wohnmischgebiete entspricht. Sie zählt zu den modernsten Anlagen Europas und ist ideal für die internen Prozessschritte beim Beschichten ausgelegt – dieser hohe Grad der Spezialisierung wäre über Outsourcing nicht erreichbar. Gegenüber dem marktgängigen Beschichten ist der Prozess hinsichtlich der Vermeidung von Bauteilbeschädigungen, Schichtverteilung, Optik und Reibbeiwerten optimiert – die qualitative Reproduzierbarkeit der 6.600 unterschiedlichen Artikel, aus denen sich das noch größere Produktspektrum herleitet, ist stets gewährleistet. Gewicht, Größe, Geometrie – dies sind nur einige der durchschnittlich zwölf Programmparameter, die für jeden Artikel im Produktionssystem hinterlegt sind. Sie sind eine wichtige Voraussetzung, um die unterschiedlichen Verbindungsteile wiederkehrend optimal zu beschichten.
Artikelspezifisch sind die Stromstärke beim Galvanisieren, die Verweildauer im Becken und das Handling klar definiert. Die Gestelle und Körbe, mit denen die Verbindungsteile in der Anlage transportiert werden, sind Eigenentwicklungen. Größere Verbindungsteile mit bis zu 2,5 kg Gewicht und empfindlichen Außengewinden stecken Mitarbeiter manuell auf Gestelle und beugen so potenziellen Gewindebeschädigungen während des Beschichtungsprozesses vor. Bei der Vorbehandlung werden die Artikel per Ultraschall gereinigt, um eventuelle Verschmutzungen der Bohrungen zu entfernen. Kleinere Bauteile werden über Trommeln dem Prozess zugeführt. Die taktweise Befüllung erfolgt über ein Förderband, um die Fallhöhen zu minimieren und prozessbedingte Beschädigungen zu verhindern. Eine deutlich reduzierte Beschichtungszeit schont das Material zusätzlich.
Zur ressourcenschonenden Produktion wird per Online-Analytik und ‑Sensorik der gesamte Galvanikprozess gesteuert und überwacht. Automatische Dosierpumpen sorgen dafür, dass produktspezifisch stets die richtige Menge an Chemikalien zugeführt wird. Die Bäder bleiben so stabil innerhalb der vorgegebenen Prozessgrenzen. Für die gleichmäßige Verteilung der Chemikalien werden diese kontinuierlich in Bewegung gehalten. Nach dem Galvanikprozess werden die Schichtdicke und die Nickeleinbaurate bei jedem Produktionslos kontrolliert. So erfahren die Artikel nachweislich eine gleichmäßige Beschichtung mit VOSS coat und sind dauerhaft gegen Korrosion geschützt.
Seit 2013 wird zudem eine Versuchsgalvanik betrieben, bei der der gesamte Galvanikprozess in Miniaturform abgebildet und ressourcenschonend veränderte Fertigungsparameter simuliert werden können. Neben der Weiterentwicklung von VOSS coat fließen hier auch Optimierungen der internen Prozesse in Bezug auf Effizienz und Nachhaltigkeit mit ein. Anwender profitieren somit von einer zukunftssicheren Oberflächenbeschichtung und kundenspezifischen Systemlösungen.
Qualität von A bis Z
Die Qualität der Produkte, ihre Maßgenauigkeit und damit ihr prozesssicherer Einsatz hängen nicht allein von der Galvanotechnik ab. Der hohe Produktstandard nimmt seinen Anfang bereits bei der Auswahl des Vormaterials, das ausschließlich von auditierten Partnern bezogen wird. Beispielsweise wird per Spektralanalyse im Wareneingang die Zusammensetzung der Werkstoffe sowie mittels eines optischen Profilprojektors, eines Konturmessgeräts oder eines Rautiefenmessers die Geometrie der Waren ermittelt. Auch Härtemessungen und die Prüfung der Elastomere beispielsweise für Dichtungsringe finden hier statt. Eine weitere Besonderheit ist die Maschinenfähigkeitsuntersuchung, die alle Artikel durchlaufen, um eine konstant hohe Produktqualität zu gewährleisten. Mittels statistischer Prozesskontrolle (SPC) wird jedes Produktionslos überwacht – sowohl in der Zerspanung als auch bei der Beschichtung. Während der Zerspanung wird der Verschleiß der Werkzeuge permanent überwacht. Als Schwester der VOSS Automotive, Anbieter von Systemlösungen für die internationale Nutzfahrzeug- und Pkw-Industrie, verfolgt auch VOSS Fluid eine Null-Fehler-Strategie, um den steigenden Anforderungen in der Fluidtechnik gerecht zu werden.
Fazit
Die Prozesssicherheit hydraulischer Systeme in mobilen und stationären Arbeitsmaschinen ist abhängig von der Auswahl der geeigneten Rohrverbindungstechnik für den jeweiligen Einsatzzweck, ihrer Korrosionsbeständigkeit und der fachgerechten Montage. Die Basis legt die VOSS Fluid GmbH mit ihrer Beratungs- und Anwendungskompetenz: Durch die technische Begleitung der Kunden in der Projektierung, dem Engineering und bei der Montage werden montagesichere Produktionsprozesse gewährleistet. Dank der eigens entwickelten Zink-Nickel-Technologie sowie modernen Fertigungs- und Qualitätsstandards erhalten Anwender Rohrverbindungen mit optimalen Montagedrehmomenten und einem hohen Korrosionsschutz. Das Resultat sind langlebige Maschinen sowie ein prozesssicheres und wirtschaftliches Hydrauliksystem.
Ein Plus an Qualität und Wirtschaftlichkeit
Ein Plus an Qualität und Wirtschaftlichkeit
Rohrverbindungskomponenten sind die „Hidden Heroes“ in mobilen und stationären Hydrauliksystemen. Denn die auf den ersten Blick eher unscheinbaren Bauteile sind oft sicherheitsrelevante Systembestandteile. Sie tragen maßgeblich zur Qualität, Effektivität und Langlebigkeit des gesamten Produktes bei. Deutlich wird dies immer dann, wenn es zu Leckagen oder anderen Funktionsbeeinträchtigungen kommt. Genau aus diesem Grund ist die Wahl der richtigen Verbindungstechnik entscheidend. Zu beachten gibt es dabei einiges. Denn trotz ihrer Normierung unterscheiden sich Rohrverbindungskomponenten deutlich in Qualität, Ausführung und Wirtschaftlichkeit.
Dauerhaft leckagefreie Verbindungsstellen erhöhen die Wirtschaftlichkeit und Sicherheit von Hydrauliksystemen und fördern ein positives Produktimage. Voraussetzung ist die optimale Verbindungstechnik für den jeweiligen Anwendungsfall. „Vor der Produktauswahl sollte immer eine konkrete Analyse der wichtigsten Systemparameter stehen“, rät Georg Rempel, Anwendungstechniker bei der VOSS Fluid GmbH. „Entscheidende Faktoren sind beispielsweise Druck, Volumenstrom, Umgebungstemperatur, äußere Einflüsse, Normung und Gesetzgebung sowie die Belastungsart.“ Ist die Entscheidungsbasis definiert, folgt die Auslegung und Auswahl der Verbindungstechnik.
Die Qual der Wahl
Die extrem hohe System- und Typenvielfalt, die der Markt bei Rohrverbindungskomponenten bereithält, bietet für nahezu jeden Anwendungsfall die passende Lösung. Damit stehen Unternehmen allerdings auch vor der Qual der Wahl. Welches System ist langfristig am zuverlässigsten? Und ist dieses auch das wirtschaftlichste? „Der Qualitätsanspruch der Anwender hat sich in den letzten Jahren dramatisch verändert“, berichtet Rempel. „Heute muss es die perfekte Lösung sein – und diese natürlich zum günstigsten Preis.“ Vor diesem Hintergrund haben Normteile an Bedeutung gewonnen. Doch trotz ihrer Standardisierung unterscheiden sie sich erheblich hinsichtlich Qualität und Wirtschaftlichkeit. Wer also Rohrverbindungskomponenten benötigt oder mit der bisherigen Lösung unzufrieden ist, sollte sich die Beratungsleistung eines Qualitätsherstellers zunutze machen. Anwendungstechniker Rempel berichtet: „Meine Erfahrung in der Kundenbetreuung zeigt, dass wir immer spürbar sicherere, haltbarere oder kostengünstigere Alternativen bieten können.“
Wirtschaftlichkeit
Ein wesentliches Kriterium bei der Auswahl des passenden Verbindungssystems ist dessen Wirtschaftlichkeit. Neben dem Einkaufspreis sollten auch die Beschaffungskosten, der Montageaufwand, die Nachhaltigkeit der Dichtfunktion und der Langzeitkorrosionsschutz einbezogen werden. Wer diese Kriterien nicht von Beginn an betrachtet, wird möglicherweise von ungeplant hohen Folgekosten überrascht und muss im schlechtesten Fall sogar einen Systemwechsel in Kauf nehmen. Das heißt konkret: Eine stringente Gesamtkostenbetrachtung kann beispielsweise zur Wahl eines durchgehend weichdichtenden Systems führen, dass im Stückpreis über den Kosten einer rein metallisch dichtenden Lösung liegt. Denn durch das Plus an Prozess- und Leckagesicherheit und die damit gewonnenen wirtschaftlichen Vorteile über den gesamten Maschinenlebenszyklus macht sich die Entscheidung bezahlt.
Sicherheit
Undichte Hydrauliksysteme sind in den meisten Fällen eine direkte Folge von Montagefehlern. Daher raten alle Hersteller, die Bedienungsanleitungen sorgfältig und genau zu beachten. Dennoch bleibt ein gewisses Restrisiko, insbesondere bei Anwendern, die mit unerfahrenem oder häufig wechselndem Personal arbeiten. Abhilfe schaffen hier ausgeklügelte Lösungen, die Fehlmontagen auf ein absolutes Minimum reduzieren oder sogar ausschließen. Das neue Schneidringsystem VOSSRingM mit dazugehörigem VOSSRing-Vormontagestutzen liefert ein solches zusätzliches Plus an Sicherheit. Neben vielen innovativen Systemvorteilen bietet es einen zuverlässigen Schutz vor Montagefehlern. Möglich macht dies ein intelligentes Anschlagkonzept, das dem Monteur den genauen Endpunkt der Vormontage mittels eines deutlich spürbaren Kraftanstiegs signalisiert.
Der Vormontageprozess wird so intuitiv am optimalen Punkt beendet – eine Übermontage ist wirksam unterbunden. Auch bei der späteren Endmontage verhindert das neue Schneidringsystem zuverlässig Fehlmontagen. „Ich rate Entscheidern, die Montagefreundlichkeit bei der Auswahl besonders gründlich zu prüfen“, ergänzt Anwendungstechniker Rempel. „Hierbei sollte der Anwender hinterfragen, welche Werkzeuge, Schulungen und welche Vor-Ort-Unterstützung der Lieferant anbietet. Ein qualitätsorientierter Hersteller wird immer wertvolle Tipps geben, die speziell auf die individuellen Fertigungsprozesse ausgerichtet sind.“
Korrosionsschutz
Unabhängig vom konkreten Einsatzzweck oder von der Abdichtungs- und Belastungsart kommt der Oberflächenbeschichtung der Rohrverbindungskomponenten eine besondere Bedeutung zu. Sie ist Voraussetzung für einen dauerhaften Korrosionsschutz sowie funktionsbeständige und damit wirtschaftliche Bauteile. Diese Faktoren prägen langfristig natürlich auch das Image des Erstausrüsters, da korrosionsbeständige Maschinen für gute Qualität stehen und einen höheren Wiederverkaufswert erzielen. VOSS Fluid entwickelte für seine Produkte eine eigene Zink-Nickel-Beschichtung: VOSS coat. Diese trotzt selbst aggressiven Medien und garantiert so die kundenseitig gewünscht hohe Korrosionsbeständigkeit. Unternehmen, die durchgängig auf VOSS Rohrverbindungskomponenten setzen, profitieren daher von einem ausnahmslos hohen Korrosionsschutz. Denn das Unternehmen stattet alle seine Produkte mit der nachhaltigen Oberfläche aus. „Generell ist natürlich auch eine Verwendung von Bauteilen unterschiedlicher Hersteller möglich“, merkt Anwendungstechniker Rempel an. „Ich rate allerdings davon ab. Unsere Produktlinien sind optimal aufeinander abgestimmt und gewährleisten somit beste Funktion und Qualität.“ Anwendertests zeigen sogar, dass selbst gleiche Oberflächentypen nicht dieselben Eigenschaften besitzen: Die Untersuchung eines führenden deutschen Landmaschinenherstellers ergab, dass keine der getesteten Rohrverbindungskomponenten so korrosionsbeständig gegen aggressive Düngemittel waren wie die mit VOSS coat beschichteten.
Qualität von A bis Z
Die Qualität der Produkte, ihre Maßgenauigkeit und damit ihr prozesssicherer Einsatz sind noch von vielen weiteren Faktoren abhängig. Der hohe Produktstandard nimmt seinen Anfang bereits bei der Auswahl des Vormaterials, das ausschließlich von auditierten Partnern bezogen werden sollte. Qualitätsbewusste Hersteller ermitteln beispielsweise im Wareneingang per Spektralanalyse die Zusammensetzung der Werkstoffe und messen die Geometrie der Waren. Auch Härtemessungen und die Prüfung der Elastomere – beispielsweise für Dichtungsringe – sollten selbstverständlich sein. „Jeder Produktionsschritt wird bei VOSS Fluid durch Qualitätssicherungsmitarbeiter kontrolliert und bei Bedarf sofort optimiert – sowohl in der Zerspanung und der Beschichtung als auch bei der Montage.“ Ziel ist dabei eine besonders hohe Produktqualität und -zuverlässigkeit, um den steigenden Anforderungen in der Fluidtechnik gerecht zu werden. Ein weiterer entscheidender Erfolgsfaktor ist die Logistikkompetenz des Lieferanten. Dieser sollte eine hohe Liefertreue gewährleisten und durch intelligente logistische Dienstleistungen zu verringerten Kosten im C-Teile-Management beitragen. Auch die weltweite Verfügbarkeit des gesamten Katalogprogramms ist von entscheidender Bedeutung. Der Verbindungstechnikspezialist sollte daher rund um den Globus ein engmaschiges Vertriebsnetzwerk betreiben und ständige Versorgungssicherheit gewährleisten.
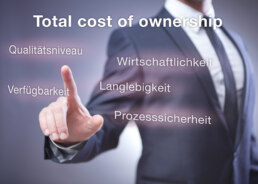
Fazit
Bei der Auswahl hydraulischer Verbindungstechnik stehen Anwender vor der Qual der Wahl. Schlussendlich muss das gesamte Leistungspaket des Herstellers überzeugen. Ein guter Lieferant beherrscht dabei die gesamte Wertschöpfungskette: vom Vormaterial über die Produktion und Oberflächenbeschichtung bis hin zur Logistik. Vor allem ist entscheidend, inwieweit der Lieferant bereit ist, den Anwender aktiv zu unterstützen. Erfahrene Hersteller verfügen über ein breites Wissensspektrum für nahezu jeden Anwendungsfall und bieten individuelle Beratung und maßgeschneiderte Lösungen.