1 Jahr VOSS Fluid Polen
Produktion undVertrieb in Legnica läuft seit einem Jahr
Wachstum am Standort Polen: VOSS Fluid zieht positive Bilanz
Sichere und effiziente Schlauchverbindungen
Sichere und effiziente Schlauchverbindungen
Ein prozesssicheres und effizientes Hydrauliksystem ist angesichts der stetig steigenden Anforderungen am Markt eine zentrale Herausforderung. Für einen zuverlässigen und langlebigen Maschineneinsatz kommt es daher auf die richtige Auswahl und ein perfektes Zusammenspiel aller Einzelkomponenten an. Mit der Erweiterung des Produktportfolios um Schlaucharmaturen bietet VOSS Fluid nun eine anforderungsgerechte Verbindungstechnik für das gesamte Leitungssystem an.
VOSS Fluid, Qualitätshersteller für Rohrverschraubungstechnik, hat sein Produktspektrum sinnvoll erweitert: Neben moderner Rohrverbindungstechnik liefert das Unternehmen nun auch sämtliche Komponenten für den Schlauchanschluss mobiler und stationärer Maschinen und Anlagen. Im Ergebnis reduzieren Anwender die Anzahl ihrer Lieferanten und erhalten darüber hinaus eine einheitliche Produktqualität auf höchstem technischem Niveau, die vor allem in Hinblick auf die Leckagesicherheit und Korrosionsbeständigkeit überzeugt. Hydraulikkomponenten aus dem Hause VOSS Fluid stehen für moderne hydraulische Verbindungstechnik aus einer Hand.
Wegbereiter für korrosionsbeständige Schlaucharmaturen
Ausschlaggebend für den flächendeckend erfolgreichen Einsatz sind ein herausragender Produktstandard, die hohe Beratungskompetenz sowie anwendungsgerechte Lösungen.
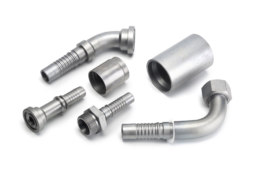
Das Sortiment an Schlaucharmaturen verfügt ebenfalls wie das gesamte Produktprogramm über die typische VOSS Zink-Nickel-Oberflächenbeschichtung. Um das hohen Qualitätsniveau dauerhaft zu halten, werden die Produkte wiederkehrend allen notwendigen Prüfungen unterzogen. Dazu gehören das hydrostatische Prüfverfahren nach EN ISO 1402 und die Druck-Impulsprüfung nach EN ISO 6803. Darüber hinaus ist die Validierungsprüfung wichtiger Bestandteil der umfassenden Serviceleistung von VOSS Fluid: Neben den gängigen Pressmaßtabellen, welche die erforderlichen Pressmaße für die Herstellung von Schlauchleitungen liefern, testet das Unternehmen individuell die vom Kunden verwendeten Schläuche verschiedenster Hersteller in Form einer sogenannten „Freiprüfung“. Durch Fertigungstoleranzen sind diese ständigen Veränderungen ausgesetzt. Daher stellt VOSS in regelmäßigen Abständen die korrekten Werte bereit und garantiert, dass die Verbindungskomponenten den Arbeitsdrücken sämtlicher Schläuche sicher standhalten. Alle Produktprüfungen können durch das eigene Prüflabor Inhouse durchgeführt werden. Aussagekräftige Daten über die Produktsicherheit fließen auf diese Weise direkt an den Kunden, der von einer umfassenden technischen Beratung und Funktionssicherheit profitiert.
Erhöhte Langlebigkeit
Was bei Rohrverbindungskomponenten maßgeblich im Vordergrund steht, ist für Schlaucharmaturen ebenfalls Standard: Eine dauerhafte Korrosionsbeständigkeit mithilfe der bewährten VOSS Zink-Nickel-Oberfläche. Durch diese Oberflächenbeschichtung wird die Funktionsfähigkeit des Bauteils um ein Vielfaches verlängert. Prüfergebnisse aus der Salzsprühnebelkammer haben ergeben, dass die Oberfläche eine vielfach höhere Beständigkeit gegenüber Rotrost aufweist als reine Verzinkungen. Mit den Zink-Nickel-beschichteten Schlaucharmaturen und Verbindungskomponenten treffen Kunden eine nachhaltige Produktentscheidung, da Bauteile dadurch langfristig wirtschaftlich im Einsatz sind und auch optisch nicht als „Qualitätsmangel“ durch den Endanwender wahrgenommen werden.
Die drei Hauptanforderungen an Schlauchleitungen
Höchstleistungen in der Hydraulik erfordern höchste Lösungskompetenz. Hydraulikschläuche bestehen aus Elastomeren, die dem Druckmedium im Innern über lange Zeit standhalten müssen. Um die Prozesssicherheit zu gewährleisten, spielen die drei Einflussfaktoren Druck, Temperatur und das eingesetzte Medium eine besondere Rolle für die hydraulische Auslegung der Maschine. Im ersten Schritt ist zu beachten, ob besondere Einbausituationen wie beispielsweise Reduzierungen oder Befestigungspunkte, die der Funktionalität der Maschinen zugutekommen, die Druckleistung behindern. Im zweiten Schritt muss der Temperaturbereich unter die Lupe genommen werden: Zu hohe Betriebstemperaturen können sich negativ auf die Bauteile auswirken.
Druck
Temperatur
eingesetztes Medium
Durch Oxidation bilden die Druckmedien schon nach relativ kurzer Einsatzdauer Säuren, welche die elastomeren Bestandteile des Systems sowie die Buntmetalle angreifen können. Zudem schleicht sich in temperaturlastigen Systemen durch Kondensation immer ein für die Anwendung nicht gern gesehener Gast ein: Wasser. Ungelöstes Wasser im Öl setzt sich in der gequollenen Innenschicht der Schlauchleitung ab. Durch ungünstige Temperatur-Druck-Verläufe besteht die Möglichkeit, dass die Wassereinlagerung verdampft. Kleine Teile des umliegenden Elastomers sprengen dabei heraus und beschädigen die Schlauchleitung im Innern. Bei diesem Phänomen spricht man von dem sogenannten Popcorning-Effekt. Der dritte Punkt bezieht sich auf das eingesetzte Medium. Die sich heute im Einsatz befindlichen Fluide reichen von Wasser-Öl-Emulsionen über Standard- und Sondermineralöle bis hin zu biologisch abbaubaren Hydraulikflüssigkeiten auf pflanzlicher, mineralischer und synthetischer Basis. Als eine Folge des Zusammenspiels von Elastomer und Fluid tritt das Quellen des Gummiwerkstoffes auf.
Nimmt dieser das eingesetzte Fluid in sich auf, vergrößert sich sein Volumen in einem unerwünschten Maße, sodass in den Innenschichten von Schlauchleitungen Schäden entstehen können und sich die Leitungsdurchmesser verengen. Um diesen unerwünschten Effekten entgegenzuwirken, ist eine durchdachte Systemauslegung und -auswahl notwendig.
Denn verengte Leitungsdurchmesser werden nicht nur durch Quellen des Hydraulikschlauches hervorgerufen. Die erste Querschnittsverengung kommt bereits durch den Schlauchnippel zustande. Weitere Verengungen können beispielsweise durch einfallende 90° gebogene Schlaucharmaturen auftreten. Diese weisen innerhalb der Biegung eine hohe Ovalität auf, wodurch Verwirbelungen und Druckverluste entstehen. Unter Einbeziehung aller notwendigen Parameter bei der Auslegung der Hydraulikanlagen werden Ausfälle und Schäden weitestgehend vermieden. Von Vorneherein wird die Frage gestellt, was die Schlauchleitung im Einsatz leisten muss: Für hochdynamische Beanspruchungen bietet VOSS ein Design für Schlaucharmaturen mit Ausreißsicherung. Diese werden durch ein spezielles Verpressverfahren mit dem Schlauch verbunden, so dass sich kein Elastomer mehr zwischen Armatur und Schlauch befindet. Von außen und innen besteht dadurch ein direkter Kontakt mit dem Stahl, wodurch der daraus resultierende Formschluss zwischen Fassung, Schlauch und Armatur das Herauswandern des Schlauches verhindert. Auch bei Druckstufenerhöhungen der Armatur werden Leckagen auf diese Weise weitestgehend vermieden.
Fazit
Mit seinem Portfolio an aufeinander abgestimmter Rohr- und Schlauchverbindungstechnik ermöglicht VOSS Fluid eine gleichbleibend hohe Qualität. Die individuellen Anforderungen für den Anschluss Rohr-zu-Schlauch immer im Blick, erhalten Kunden vielfältige Hydraulikkomponenten, die auf Druck, Temperatur und Fluid optimal angepasst sind und so eine hohe Effizienz und Langlebigkeit im Betrieb erzielen.
Sichere Hydraulik dank hochwertiger Verbindungstechnik
Sichere Hydraulik dank hochwertiger Verbindungstechnik
Hohe Wirkungsgrade, wechselnde Temperaturbedingungen und häufige Lastwechsel – Hydrauliksysteme stationärer und mobiler Arbeitsmaschinen sind stetigen Belastungen ausgesetzt. Um langfristig die größtmögliche Funktionsfähigkeit zu gewährleisten, ist eine korrosionsbeständige und präzise Verbindungstechnik unerlässlich.
Kleine Komponenten mit großer Systemfunktion: Die Prozesssicherheit hydraulischer Verbindungstechnik ist branchenübergreifend ausschlaggebend für den zuverlässigen und wirtschaftlichen Betrieb von modernen Arbeitsmaschinen. Ein zentraler Aspekt ist dabei das Streben nach mehr Energieeffizienz – doch mit den Wirkungsgraden nehmen auch die Belastungen in der Fluidtechnik zu. Damit permanent beanspruchte Anlagen wie Kunststoffspritzgießmaschinen und Großbagger im Bergbau auch unter härteren Bedingungen zuverlässig funktionieren, sind Komponenten entsprechend der Anforderung an die Leckagesicherheit der Verbindungsstelle und mit einem beständigen Korrosionsschutz notwendig. Für den Anwender bedeutet das: Neben der Auswahl systemgerechter Verbindungskomponenten stehen eine fachgerechte Montage sowie die Wahl eines kompetenten Zulieferers im Mittelpunkt.
Die VOSS Fluid GmbH ist Hersteller von Rohrverbindungssystemen und Systempartner des internationalen Maschinenbaus. Das Produktportfolio umfasst Rohrverbindungen für die Stationär- und Mobilhydraulik, darunter Schneidring- und Bördelverschraubungen, Rohrumformsysteme, Flanschverbindungen, Ventile und Zubehör. VOSS Fluid verfügt über langjährige Kompetenz in der Fertigung von Verbindungsteilen gemäß den Anforderungen der Kunden und setzt diese in der Entwicklung der Systemlösungen und der technischen Beratung ihrer Kunden gezielt ein. Das Ergebnis sind gleichbleibend hochwertige Bauteile, ein hoher Korrosionsschutz sowie eine fachgerechte, zeiteffiziente Montierbarkeit der Komponenten und langzeitdichte Hydrauliksysteme.
"Oberflächliche" Qualität mit fachlicher Tiefe
Eine zentrale, qualitative Bedingung ist die Beschichtung der Rohrverbindungen. Sie ist Voraussetzung für einen dauerhaften Korrosionsschutz sowie funktionsbeständige und damit wirtschaftliche Bauteile: VOSS Fluid setzt hierbei für alle Rohrverschraubungen die hauseigene, nachhaltige Zink-Nickel-Beschichtung VOSS coat ein. Diese erfüllt sämtliche Vorgaben der EU-Altauto-Richtlinie, die seit 2007 Chrom-VI-haltige Oberflächen untersagt. Gemeinsam mit unabhängigen Forschungsinstituten und Universitäten, wie der Fachhochschule Aalen, wurde ein Korrosionsschutz entwickelt, der im Vergleich der Basisschichten etwa um ein Zehnfaches besser ist als konventionell eingesetzte Zinkschichten. Anders als reine Zinkoberflächen bildet Zink-Nickel keinen ausgeprägten Weißrost bei der Korrosion, sondern erzeugt lediglich einen leichten Grauschleier.
Die in der EG-Verordnung 1907/2006 aufgeführten Grenzwerte zur Bestimmung der Nickellässigkeit von Produkten, die in direkten und länger andauernden Kontakt mit der Haut kommen, werden um das 50-Fache unterschritten. Im direkten Vergleich der VOSS coat Oberfläche mit einer 2-Euro-Münze wird dieser Grenzwert sogar um das 2.230-Fache unterschritten. Die Oberfläche ist durch den harten Nickelanteil nicht nur umweltverträglich, sondern auch verschleißfester gegenüber mechanischen Belastungen, denen Hydraulikverschraubungen vom Transport über die Montage bis zum Einsatz ausgesetzt sind.
VOSS coat besteht aus einer Zink-Nickel-Basisschicht, die anschließend passiviert und abschließend versiegelt wird. Diese drei Schichten verhindern die Korrosion des Grundwerkstoffs und werten die Verbindungskomponenten nachhaltig auf. Nach dem VDMA-Einheitsblatt 24576 erreicht die Zink-Nickel-Oberfläche die höchste Korrosionsbeständigkeitsklasse K5. Diese bezeichnet die Schutzleistung der Oberfläche, die eine Beständigkeit von mindestens 720 Stunden gegen Rotrost und mindestens 360 Stunden gegen Weißrost nachweist.
Unter Laborbedingungen mit unmontierten Teilen wurde im Salzsprühnebeltest nach DIN EN ISO 9227 sogar eine Korrosionsbeständigkeit von mehr als 2.000 Stunden erreicht. Im Praxistest mit Zufallsware aus der laufenden Produktion wurde nach deren Handling und Montage bewiesen, dass auch bei 1.000 Stunden keine Grundmetallkorrosion auftritt.
Für optimale Montagedrehmomente werden die Reibbeiwerte in der Entwicklung und Produktion für Schneidringverschraubungen laufend verbessert: Dadurch sind diese deutlich geringer als bei anderen Zink-Nickel-Beschichtungen. Je nach Verbindungsbauteil werden ein Gleitmittel und eine partielle Innenbeschichtung eingesetzt, beispielsweise bei Überwurfmuttern. Montagesichere Produktionsprozesse beim Kunden unterstützen erfahrene Anwendungstechniker, welche die Monteure und Instandhalter begleiten – von der Auswahl der systemgerechten Hydraulikverschraubung über Schulungen rund um leckagefreie Verbindungen bis zu regelmäßigen Montageaudits.
Know-how-Vorsprung: In-house-Galvanik
Grundlegende Voraussetzung für die qualitativ hochwertige Beschichtung der Rohrverbindungen ist die werkseigene Galvanik, die einem hohen technologischen Standard sowie den aktuellen Umweltbestimmungen für Wohnmischgebiete entspricht. Sie zählt zu den modernsten Anlagen Europas und ist ideal für die internen Prozessschritte beim Beschichten ausgelegt – dieser hohe Grad der Spezialisierung wäre über Outsourcing nicht erreichbar. Gegenüber dem marktgängigen Beschichten ist der Prozess hinsichtlich der Vermeidung von Bauteilbeschädigungen, Schichtverteilung, Optik und Reibbeiwerten optimiert – die qualitative Reproduzierbarkeit der 6.600 unterschiedlichen Artikel, aus denen sich das noch größere Produktspektrum herleitet, ist stets gewährleistet. Gewicht, Größe, Geometrie – dies sind nur einige der durchschnittlich zwölf Programmparameter, die für jeden Artikel im Produktionssystem hinterlegt sind. Sie sind eine wichtige Voraussetzung, um die unterschiedlichen Verbindungsteile wiederkehrend optimal zu beschichten.
Artikelspezifisch sind die Stromstärke beim Galvanisieren, die Verweildauer im Becken und das Handling klar definiert. Die Gestelle und Körbe, mit denen die Verbindungsteile in der Anlage transportiert werden, sind Eigenentwicklungen. Größere Verbindungsteile mit bis zu 2,5 kg Gewicht und empfindlichen Außengewinden stecken Mitarbeiter manuell auf Gestelle und beugen so potenziellen Gewindebeschädigungen während des Beschichtungsprozesses vor. Bei der Vorbehandlung werden die Artikel per Ultraschall gereinigt, um eventuelle Verschmutzungen der Bohrungen zu entfernen. Kleinere Bauteile werden über Trommeln dem Prozess zugeführt. Die taktweise Befüllung erfolgt über ein Förderband, um die Fallhöhen zu minimieren und prozessbedingte Beschädigungen zu verhindern. Eine deutlich reduzierte Beschichtungszeit schont das Material zusätzlich.
Zur ressourcenschonenden Produktion wird per Online-Analytik und ‑Sensorik der gesamte Galvanikprozess gesteuert und überwacht. Automatische Dosierpumpen sorgen dafür, dass produktspezifisch stets die richtige Menge an Chemikalien zugeführt wird. Die Bäder bleiben so stabil innerhalb der vorgegebenen Prozessgrenzen. Für die gleichmäßige Verteilung der Chemikalien werden diese kontinuierlich in Bewegung gehalten. Nach dem Galvanikprozess werden die Schichtdicke und die Nickeleinbaurate bei jedem Produktionslos kontrolliert. So erfahren die Artikel nachweislich eine gleichmäßige Beschichtung mit VOSS coat und sind dauerhaft gegen Korrosion geschützt.
Seit 2013 wird zudem eine Versuchsgalvanik betrieben, bei der der gesamte Galvanikprozess in Miniaturform abgebildet und ressourcenschonend veränderte Fertigungsparameter simuliert werden können. Neben der Weiterentwicklung von VOSS coat fließen hier auch Optimierungen der internen Prozesse in Bezug auf Effizienz und Nachhaltigkeit mit ein. Anwender profitieren somit von einer zukunftssicheren Oberflächenbeschichtung und kundenspezifischen Systemlösungen.
Qualität von A bis Z
Die Qualität der Produkte, ihre Maßgenauigkeit und damit ihr prozesssicherer Einsatz hängen nicht allein von der Galvanotechnik ab. Der hohe Produktstandard nimmt seinen Anfang bereits bei der Auswahl des Vormaterials, das ausschließlich von auditierten Partnern bezogen wird. Beispielsweise wird per Spektralanalyse im Wareneingang die Zusammensetzung der Werkstoffe sowie mittels eines optischen Profilprojektors, eines Konturmessgeräts oder eines Rautiefenmessers die Geometrie der Waren ermittelt. Auch Härtemessungen und die Prüfung der Elastomere beispielsweise für Dichtungsringe finden hier statt. Eine weitere Besonderheit ist die Maschinenfähigkeitsuntersuchung, die alle Artikel durchlaufen, um eine konstant hohe Produktqualität zu gewährleisten. Mittels statistischer Prozesskontrolle (SPC) wird jedes Produktionslos überwacht – sowohl in der Zerspanung als auch bei der Beschichtung. Während der Zerspanung wird der Verschleiß der Werkzeuge permanent überwacht. Als Schwester der VOSS Automotive, Anbieter von Systemlösungen für die internationale Nutzfahrzeug- und Pkw-Industrie, verfolgt auch VOSS Fluid eine Null-Fehler-Strategie, um den steigenden Anforderungen in der Fluidtechnik gerecht zu werden.
Fazit
Die Prozesssicherheit hydraulischer Systeme in mobilen und stationären Arbeitsmaschinen ist abhängig von der Auswahl der geeigneten Rohrverbindungstechnik für den jeweiligen Einsatzzweck, ihrer Korrosionsbeständigkeit und der fachgerechten Montage. Die Basis legt die VOSS Fluid GmbH mit ihrer Beratungs- und Anwendungskompetenz: Durch die technische Begleitung der Kunden in der Projektierung, dem Engineering und bei der Montage werden montagesichere Produktionsprozesse gewährleistet. Dank der eigens entwickelten Zink-Nickel-Technologie sowie modernen Fertigungs- und Qualitätsstandards erhalten Anwender Rohrverbindungen mit optimalen Montagedrehmomenten und einem hohen Korrosionsschutz. Das Resultat sind langlebige Maschinen sowie ein prozesssicheres und wirtschaftliches Hydrauliksystem.
Ein Plus an Qualität und Wirtschaftlichkeit
Ein Plus an Qualität und Wirtschaftlichkeit
Rohrverbindungskomponenten sind die „Hidden Heroes“ in mobilen und stationären Hydrauliksystemen. Denn die auf den ersten Blick eher unscheinbaren Bauteile sind oft sicherheitsrelevante Systembestandteile. Sie tragen maßgeblich zur Qualität, Effektivität und Langlebigkeit des gesamten Produktes bei. Deutlich wird dies immer dann, wenn es zu Leckagen oder anderen Funktionsbeeinträchtigungen kommt. Genau aus diesem Grund ist die Wahl der richtigen Verbindungstechnik entscheidend. Zu beachten gibt es dabei einiges. Denn trotz ihrer Normierung unterscheiden sich Rohrverbindungskomponenten deutlich in Qualität, Ausführung und Wirtschaftlichkeit.
Dauerhaft leckagefreie Verbindungsstellen erhöhen die Wirtschaftlichkeit und Sicherheit von Hydrauliksystemen und fördern ein positives Produktimage. Voraussetzung ist die optimale Verbindungstechnik für den jeweiligen Anwendungsfall. „Vor der Produktauswahl sollte immer eine konkrete Analyse der wichtigsten Systemparameter stehen“, rät Georg Rempel, Anwendungstechniker bei der VOSS Fluid GmbH. „Entscheidende Faktoren sind beispielsweise Druck, Volumenstrom, Umgebungstemperatur, äußere Einflüsse, Normung und Gesetzgebung sowie die Belastungsart.“ Ist die Entscheidungsbasis definiert, folgt die Auslegung und Auswahl der Verbindungstechnik.
Die Qual der Wahl
Die extrem hohe System- und Typenvielfalt, die der Markt bei Rohrverbindungskomponenten bereithält, bietet für nahezu jeden Anwendungsfall die passende Lösung. Damit stehen Unternehmen allerdings auch vor der Qual der Wahl. Welches System ist langfristig am zuverlässigsten? Und ist dieses auch das wirtschaftlichste? „Der Qualitätsanspruch der Anwender hat sich in den letzten Jahren dramatisch verändert“, berichtet Rempel. „Heute muss es die perfekte Lösung sein – und diese natürlich zum günstigsten Preis.“ Vor diesem Hintergrund haben Normteile an Bedeutung gewonnen. Doch trotz ihrer Standardisierung unterscheiden sie sich erheblich hinsichtlich Qualität und Wirtschaftlichkeit. Wer also Rohrverbindungskomponenten benötigt oder mit der bisherigen Lösung unzufrieden ist, sollte sich die Beratungsleistung eines Qualitätsherstellers zunutze machen. Anwendungstechniker Rempel berichtet: „Meine Erfahrung in der Kundenbetreuung zeigt, dass wir immer spürbar sicherere, haltbarere oder kostengünstigere Alternativen bieten können.“
Wirtschaftlichkeit
Ein wesentliches Kriterium bei der Auswahl des passenden Verbindungssystems ist dessen Wirtschaftlichkeit. Neben dem Einkaufspreis sollten auch die Beschaffungskosten, der Montageaufwand, die Nachhaltigkeit der Dichtfunktion und der Langzeitkorrosionsschutz einbezogen werden. Wer diese Kriterien nicht von Beginn an betrachtet, wird möglicherweise von ungeplant hohen Folgekosten überrascht und muss im schlechtesten Fall sogar einen Systemwechsel in Kauf nehmen. Das heißt konkret: Eine stringente Gesamtkostenbetrachtung kann beispielsweise zur Wahl eines durchgehend weichdichtenden Systems führen, dass im Stückpreis über den Kosten einer rein metallisch dichtenden Lösung liegt. Denn durch das Plus an Prozess- und Leckagesicherheit und die damit gewonnenen wirtschaftlichen Vorteile über den gesamten Maschinenlebenszyklus macht sich die Entscheidung bezahlt.
Sicherheit
Undichte Hydrauliksysteme sind in den meisten Fällen eine direkte Folge von Montagefehlern. Daher raten alle Hersteller, die Bedienungsanleitungen sorgfältig und genau zu beachten. Dennoch bleibt ein gewisses Restrisiko, insbesondere bei Anwendern, die mit unerfahrenem oder häufig wechselndem Personal arbeiten. Abhilfe schaffen hier ausgeklügelte Lösungen, die Fehlmontagen auf ein absolutes Minimum reduzieren oder sogar ausschließen. Das neue Schneidringsystem VOSSRingM mit dazugehörigem VOSSRing-Vormontagestutzen liefert ein solches zusätzliches Plus an Sicherheit. Neben vielen innovativen Systemvorteilen bietet es einen zuverlässigen Schutz vor Montagefehlern. Möglich macht dies ein intelligentes Anschlagkonzept, das dem Monteur den genauen Endpunkt der Vormontage mittels eines deutlich spürbaren Kraftanstiegs signalisiert.
Der Vormontageprozess wird so intuitiv am optimalen Punkt beendet – eine Übermontage ist wirksam unterbunden. Auch bei der späteren Endmontage verhindert das neue Schneidringsystem zuverlässig Fehlmontagen. „Ich rate Entscheidern, die Montagefreundlichkeit bei der Auswahl besonders gründlich zu prüfen“, ergänzt Anwendungstechniker Rempel. „Hierbei sollte der Anwender hinterfragen, welche Werkzeuge, Schulungen und welche Vor-Ort-Unterstützung der Lieferant anbietet. Ein qualitätsorientierter Hersteller wird immer wertvolle Tipps geben, die speziell auf die individuellen Fertigungsprozesse ausgerichtet sind.“
Korrosionsschutz
Unabhängig vom konkreten Einsatzzweck oder von der Abdichtungs- und Belastungsart kommt der Oberflächenbeschichtung der Rohrverbindungskomponenten eine besondere Bedeutung zu. Sie ist Voraussetzung für einen dauerhaften Korrosionsschutz sowie funktionsbeständige und damit wirtschaftliche Bauteile. Diese Faktoren prägen langfristig natürlich auch das Image des Erstausrüsters, da korrosionsbeständige Maschinen für gute Qualität stehen und einen höheren Wiederverkaufswert erzielen. VOSS Fluid entwickelte für seine Produkte eine eigene Zink-Nickel-Beschichtung: VOSS coat. Diese trotzt selbst aggressiven Medien und garantiert so die kundenseitig gewünscht hohe Korrosionsbeständigkeit. Unternehmen, die durchgängig auf VOSS Rohrverbindungskomponenten setzen, profitieren daher von einem ausnahmslos hohen Korrosionsschutz. Denn das Unternehmen stattet alle seine Produkte mit der nachhaltigen Oberfläche aus. „Generell ist natürlich auch eine Verwendung von Bauteilen unterschiedlicher Hersteller möglich“, merkt Anwendungstechniker Rempel an. „Ich rate allerdings davon ab. Unsere Produktlinien sind optimal aufeinander abgestimmt und gewährleisten somit beste Funktion und Qualität.“ Anwendertests zeigen sogar, dass selbst gleiche Oberflächentypen nicht dieselben Eigenschaften besitzen: Die Untersuchung eines führenden deutschen Landmaschinenherstellers ergab, dass keine der getesteten Rohrverbindungskomponenten so korrosionsbeständig gegen aggressive Düngemittel waren wie die mit VOSS coat beschichteten.
Qualität von A bis Z
Die Qualität der Produkte, ihre Maßgenauigkeit und damit ihr prozesssicherer Einsatz sind noch von vielen weiteren Faktoren abhängig. Der hohe Produktstandard nimmt seinen Anfang bereits bei der Auswahl des Vormaterials, das ausschließlich von auditierten Partnern bezogen werden sollte. Qualitätsbewusste Hersteller ermitteln beispielsweise im Wareneingang per Spektralanalyse die Zusammensetzung der Werkstoffe und messen die Geometrie der Waren. Auch Härtemessungen und die Prüfung der Elastomere – beispielsweise für Dichtungsringe – sollten selbstverständlich sein. „Jeder Produktionsschritt wird bei VOSS Fluid durch Qualitätssicherungsmitarbeiter kontrolliert und bei Bedarf sofort optimiert – sowohl in der Zerspanung und der Beschichtung als auch bei der Montage.“ Ziel ist dabei eine besonders hohe Produktqualität und -zuverlässigkeit, um den steigenden Anforderungen in der Fluidtechnik gerecht zu werden. Ein weiterer entscheidender Erfolgsfaktor ist die Logistikkompetenz des Lieferanten. Dieser sollte eine hohe Liefertreue gewährleisten und durch intelligente logistische Dienstleistungen zu verringerten Kosten im C-Teile-Management beitragen. Auch die weltweite Verfügbarkeit des gesamten Katalogprogramms ist von entscheidender Bedeutung. Der Verbindungstechnikspezialist sollte daher rund um den Globus ein engmaschiges Vertriebsnetzwerk betreiben und ständige Versorgungssicherheit gewährleisten.
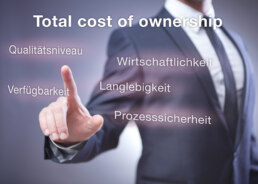
Fazit
Bei der Auswahl hydraulischer Verbindungstechnik stehen Anwender vor der Qual der Wahl. Schlussendlich muss das gesamte Leistungspaket des Herstellers überzeugen. Ein guter Lieferant beherrscht dabei die gesamte Wertschöpfungskette: vom Vormaterial über die Produktion und Oberflächenbeschichtung bis hin zur Logistik. Vor allem ist entscheidend, inwieweit der Lieferant bereit ist, den Anwender aktiv zu unterstützen. Erfahrene Hersteller verfügen über ein breites Wissensspektrum für nahezu jeden Anwendungsfall und bieten individuelle Beratung und maßgeschneiderte Lösungen.
VOSS Fluid ist "Top-Arbeitgeber" im Mittelstand
Deutschlandweite Studie von FOCUS-BUSINESS
VOSS Fluid ist „Top-Arbeitgeber“ im Mittelstand
Keine Chance für korrosiven Flüssigdünger
Keine Chance für korrosiven Flüssigdünger
Ein dauerhafter Betrieb von Bodenbearbeitungs- und Sämaschinen ist die Voraussetzung für ein zeiteffizientes und ertragreiches Wirtschaften in der Landwirtschaft. Wichtige Bedingung: Die Maschinen müssen korrosionsbeständig gegenüber Dünger, Regen und Frost sein. Das gilt besonders für funktionskritische Verbindungsteile der Maschinenhydraulik. Wenn das Bauteil nicht optimal auf die Systemanforderungen abgestimmt oder falsch montiert ist, treten hier schnell Leckagen auf.
Die Landwirtschaft ist geprägt von Preisdruck: Betriebe müssen eine hohe Arbeitsproduktivität erreichen – zusätzlich erfordern Umweltauflagen der Europäischen Union ein ressourcenschonendes Bewirtschaften des ländlichen Raums. Einer der führenden Hersteller anforderungsgerechter Maschinen und fortschrittlicher Komponenten für die Bodenbearbeitung, Sätechnik und den Pflanzenschutz ist die Horsch Maschinen GmbH.
Neue Qualitätsstandards in der Hydraulik
Innerhalb der letzten Jahre verzeichnete Horsch einen zunehmenden Bedarf an Düngemaschinen – hier sind die Anforderungen an den Korrosionsschutz der verbauten Teile besonders hoch. „Die Korrosionsbeständigkeit gegen Flüssigdünger und Düngerstaub ist extrem wichtig für unsere Kunden. Sie erwarten einsatzsichere, aber auch optisch einwandfreie Maschinen – und das selbst noch nach Jahren des Betriebs“, betont Thomas Prüll aus der Forschung und Entwicklung bei Horsch. Um Kunden auch in der Fluidtechnik einen zukunftssicheren und gleichbleibend hohen Standard zu gewährleisten, erklärte Horsch die VOSS Fluid GmbH zum Standardzulieferer für die hydraulische Verbindungstechnik. „VOSS Fluid überzeugte uns mit der Zink-Nickel-Beschichtung, die mit ihrem hohen Korrosionsschutz am Markt maßgebend ist“, begründet Thomas Prüll.
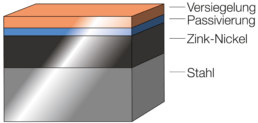
"VOSS Fluid überzeugte uns mit der Zink-Nickel-Beschichtung, die mit ihrem hohen Korrosionsschutz am Markt maßgebend ist."
– Thomas Prüll | Forschung und Entwicklung Hirsch Maschinen GmbH
Ausschlaggebende Argumente für Horsch: VOSS coat übertrifft sogar die höchste Korrosionsschutzklasse K5 des VDMA-Einheitsblattes 24576, in dem eine Rotrostbeständigkeit der Oberfläche von mindestens 720 Stunden gefordert wird. Zudem bildet sich, anders als bei reinen Zinkoberflächen, anstelle von ausgeprägtem Weißrost nur ein leichter, optisch unauffälliger Grauschleier. Mit VOSS coat beschichtete, unmontierte Teile erzielen im Salzsprühnebeltest eine Korrosionsbeständigkeit von mehr als 2.000 Stunden. Aber auch im Praxistest unter realen Bedingungen stellt die Oberfläche ihre hohe Beständigkeit unter Beweis. Dafür durchlief Zufallsware aus der laufenden Produktion die typischen Arbeitsprozesse vom Transport über die Lagerung bis zur Montage mit handelsüblichen Werkzeugen. Trotz mechanischer Beanspruchung zeigte sich an den Verbindungsteilen auch nach 1.000 Stunden keine Grundmetallkorrosion. Um sich der nachhaltigen Eignung auch bezüglich der Anforderungen in der Agrartechnik zu versichern, nahm Horsch VOSS coat genauer unter die Lupe. „Die Ergebnisse aus dem Salzsprühnebeltest sind für uns nur bedingt aussagekräftig“, so Prüll. „Die tatsächlichen Auswirkungen von Montage, Dünger, Temperatur und Feuchtigkeit auf die Korrosionsbeständigkeit zeigen sich erst auf dem Acker.“ Die Bedingungen im Einsatz stellen sogar einen wirkungsvollen Korrosionsschutz auf die Probe: Kommen freiliegende Teile in Kontakt mit Mineral- oder Nitratdüngern, kann dies zu verstärkter Korrosion führen.
Daher prüfen die Entwickler von Horsch in einem eigenen Bewitterungstest seit November 2013, wie sich Verschraubungen verschiedener Hersteller und unterschiedliche Oberflächen über einen längeren Zeitraum verhalten. Um die Praxisbedingungen realistisch nachzubilden, montierte Horsch die Verschraubungen, befestigte sie an einem Gestell und setzte sie der natürlichen Bewitterung aus. Über zwei Monate besprühten die Entwickler die Bauteile jeden Werktag mit einer gängigen und für ihre korrodierende Wirkung bekannten Flüssigdüngerlösung. Den Vergleich traten Bauteile mit A3C-Beschichtung und Zink-Nickel-Oberfläche sowie Verbindungsstücke aus Edelstahl an. Schon nach kurzer Zeit zeigte sich auf den verzinkten, gelbchromatierten Oberflächen und den handelsüblichen Zink-Nickel-Beschichtungen ganzflächig Rotrost. Auf der Verbindungstechnik von VOSS Fluid sind dagegen auch sechs Monate nach Testbeginn nur marginale Spuren von Korrosion zu erkennen. Damit schneidet VOSS coat im direkten Vergleich mit anderen Zink-Nickel-Oberflächen am besten ab – ein Hinweis darauf, dass die hohe Korrosionsbeständigkeit nicht allein auf die Beschichtung zurückzuführen ist. Das Resultat: Die VOSS Rohrverbindungen sind auch unter realen Bedingungen dauerhaft funktionsfähig und gleichzeitig eine wirtschaftliche Alternative zu Edelstahl.
Hohe Fertigungs- und Anwendungskompetenz
Der hohe Korrosionsschutz der Verschraubungen ist begründet in der von VOSS Fluid eigens entwickelten, nachhaltigen Oberflächentechnologie und der langjährigen Erfahrung in der Produktion und Anwendung von Rohrverbindungen. Der Schichtaufbau von VOSS coat ist auf den ersten Blick vergleichbar mit marktüblichen Zink-Nickel-Beschichtungen. Er besteht aus einer Zink-Nickel-Basisschicht, die anschließend passiviert und versiegelt wird. Zentrales Unterscheidungsmerkmal ist die Gestaltung der Beschichtungsprozesse, die der Hersteller aus Wipperfürth kontinuierlich optimiert:
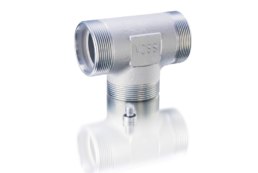
Voraussetzung ist die eigene Galvanik, in der nur Rohrverschraubungen beschichtet werden. So hat sich der Verbindungsexperte auf die effiziente und schonende Reproduzierbarkeit jedes seiner rund 16.000 Artikel spezialisiert – mehr als hundert Millionen Teile laufen jährlich durch die Galvanik. Dank der eigens für jedes Produkt hinterlegten Prozessparameter erreicht VOSS hochwertige Ergebnisse hinsichtlich einer gleichmäßigen Schichtverteilung, der Optik und der Reibbeiwerte. Schulungen zur leckagefreien Montage der Verbindungstechnik gewährleisten Horsch zusätzlich einen prozesssicheren Einbau ins Hydrauliksystem. Reklamationen in Bezug auf die Verschraubung gehören seit dem Wechsel zu VOSS Fluid der Vergangenheit an.
In der Verbindung liegt die Kraft
In der Verbindung liegt die Kraft
Was haben Medizinprodukte und Autos gemeinsam? Beides sind Hightechentwicklungen, die ohne hochpräzise gefertigte Bauteile nicht funktionieren. Möglich ist eine solch genaue Bearbeitung mit den Werkzeugmaschinen der GROB-Gruppe. Bei der spanenden Fertigung wirken extrem hohe Kräfte auf die Werkstücke ein. Sämtliche Vorrichtungen für die Werkzeug- und Werkstückspannungen werden daher mit einer ausgefeilten Hydraulik betrieben. Bei den Hydraulikverbindungen vertraut GROB auf das Rohrumformsystem VOSSFormSQR in Kombination mit der prozesssicheren Umformmaschine VOSSForm 100. Darüber hinaus setzt das Unternehmen weitere Komponenten von VOSS Fluid ein, wie leckagesichere Schneidringverschraubungen.
Der Name GROB steht international für Werkzeugmaschinen höchster Präzision. In der Automobilindustrie, im Flugzeugbau, in der Medizintechnik und in einer Reihe weiterer Branchen genießt das Familienunternehmen mit Sitz in Mindelheim großes Vertrauen. Das Produktportfolio gliedert sich in die Bereiche Systemmaschinen, Universalmaschinen für die spanende Bearbeitung, Anlagen für die Elektromobilität, komplette Montageanlagen, bestehend aus modular aufgebauten Bearbeitungszentren und Sondermaschinen, sowie den Bereich neue Technologien. Weltweit erwirtschaftet die GROB-Gruppe mit knapp 6.000 Mitarbeitern auf vier Kontinenten einen Umsatz von rund 1,3 Mrd. Euro. „Wir stellen hohe Anforderungen an uns selbst und haben den Anspruch, die Nummer 1 zu sein. Das erfordert ständige technische Innovationen. Genau das Gleiche erwarten wir auch von unseren Zulieferern“, erläutert Anton Kuhn, Abteilungsleiter Fluid-Konstruktion bei GROB.
Universalmaschinen von GROB
GROB 5-Achs Universalmaschinen lassen sich in den unterschiedlichsten Bereichen einsetzen – wie beispielsweise dem Formen- und Prototypenbau mit anspruchsvollen, hochgenauen Geometrien mit Raumschrägen und Raumbohrungen. Die Werkzeugmaschinen arbeiten auf einen tausendstel Millimeter genau. Eine solch exakte Bearbeitung setzt voraus, dass die Werkstücke in komplexen Spannvorrichtungen positioniert und fixiert werden. Dabei kommt der Hydraulik eine besondere Bedeutung zu. Sie hat die Aufgabe, Werkzeuge zu spannen und Gewichte auszugleichen. Außerdem sorgt sie für die Klemmung von Achsen und Spindeln. In der Regel wirken bis zu 120 bar auf die Hydraulikverbindungen, bei Druckspitzen vereinzelt sogar bis zu 300 bar. Rund 70 bis 100 m Hydraulikleitung sind in den Werkzeugmaschinen der G-Reihe verbaut, hinzu kommen unzählige Verbindungen. Gemäß den von GROB definierten Qualitätsstandards müssen die Verbindungselemente zwischen den einzelnen Hydraulikrohren höchste Leckagesicherheit aufweisen. „Die Hydraulik ist ein sensibler Bestandteil unserer Werkzeugmaschinen, denn hydraulische Antriebe sorgen für höchste Präzision bei den Werkzeugbewegungen. Daher muss die Verbindungstechnik zuverlässig und dauerhaft leckagefrei sein“, betont Kuhn. Neben der Leckagefreiheit sind eine einfache Handhabung und ein attraktives Preis-Leistungs-Verhältnis weitere Anforderungen, die GROB an seine Lieferanten von Hydraulikverbindungen stellt.
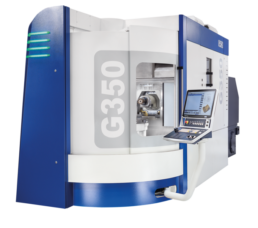
Einfach leckagefrei
Mehrheitlich setzt GROB die Verbindungslösung VOSSFormSQR ein. Neben der Qualität war die einfache Handhabung von VOSSFormSQR ein ausschlaggebender Grund. Um eine sichere Verbindung zu erzeugen, sind nur wenige Arbeitsschritte erforderlich: Zunächst formt die Umformmaschine VOSSForm 100 binnen wenigen Sekunden an das Ende eines Hydraulikrohres eine 24° Rohrkontur an. Dazu muss das Rohrende bis zur Anschlagplatte in die Maschine geschoben werden. Da ein Innendorn am Ende des Stauchkopfes die Einschnürung des Rohres verhindert, bleibt der Rohrinnendurchmesser vollständig erhalten und Druckverluste durch Einwölbungen werden verhindert.
Zusammen mit einer Weichdichtung aus FKM und einer spezifischen SQR-Funktionsmutter entsteht eine einfache und hochwertige Verbindung. Besonders die Montagesicherheit durch den Schutz vor Übermontage ist für GROB ein entscheidender Vorteil des Systems: Bei der Endmontage schlägt die Stirnseite des mit VOSSFormSQR umgeformten Rohrendes gegen den Stutzengrund im Verschraubungskörper. Beim Anzug der Funktionsmutter werden diese Komponenten fest miteinander verspannt, wobei ein spürbarer Kraftanstieg dem Monteur das Erreichen des Montageendes signalisiert. „Ein Großteil aller auftretenden Leckagen entsteht durch falsche Montage. Mit VOSSFormSQR reduzieren wir dieses Risiko entscheidend. Deshalb ist diese Technik unserer Ansicht nach die sicherste und beste Verbindung. Auch unsere Mitarbeiter sind mit dem System zufrieden“, sagt Kuhn. Weltweit hat GROB zwölf VOSSForm 100 Umformmaschinen im Einsatz.
Weichdichtende Schneidringe
Ergänzend zur Rohrumformung mit VOSSForm 100 setzt das international agierende Familienunternehmen auch den weichdichtenden Schneidring ES-4 aus dem Hause VOSS ein. Diesen verbaut GROB insbesondere in den Systemmaschinen für die Automobilindustrie. Das Funktionsprinzip basiert auf einer Zwei-Schneiden-Technologie mit zwei zusätzlichen Weichdichtungen. Die beiden Weichdichtungen sind eine Besonderheit des ES-4: Mithilfe der vollständig spaltfrei gekammerten Weichdichtung garantiert der ES-4 auch bei einem eventuellen Nachlassen der metallischen Dichtung eine trockene und schwitzfreie Verbindung. Selbst Vibrationen hält die Verbindung auf diese Weise stand. Die spaltfreie Kammerung der Dichtung erreicht der Anwender durch die Blockmontage. Diese vermeidet, dass der Ring zu tief einschneidet – eine Übermontage wird somit verhindert.
Service und Schulungen
An seinem Partner VOSS Fluid schätzt GROB nicht nur die hohe Qualität der Produkt und deren einfache und sichere Handhabung, sondern auch den Service. „VOSS Fluid ist ein agiles Unternehmen und kundennah aufgestellt“, beschreibt Kuhn. Um die geforderten kurzen Reaktionszeiten zu gewährleisten, hält VOSS Fluid zusammen mit ihrem Premium-Vertriebs- und -Servicepartner, der Fritz Stiefel GmbH, jeweils einen Teil des benötigten Materials bereit. GROB profitiert nicht nur von hoher Termin- und Liefertreue, sondern auch von Produkt- und Montageschulungen. Gemeinsam mit ihrem Vertriebs- und Servicepartner trainiert VOSS Fluid die Monteure des Maschinenbauers regelmäßig in der korrekten Anwendung der VOSS Lösungen.
Kanban-Service durch die Stiefel GmbH
Seit mehr als 13 Jahren leistet der VOSS Fluid Partner Stiefel für GROB einen Kanban-Service. Dieser ist über ein klassisches Zwei-Kisten-System mit einer definierten Mindestfüllmenge organisiert. Dreimal pro Woche tauscht die Stiefel GmbH die Behälter aus. Einmal pro Woche ist zudem ein Fachmann aus dem Bereich der Hydrauliktechnik vor Ort und unterstützt GROB in allen Fragen zu den VOSS Lösungen. „Seit dreizehn Jahren arbeiten wir mit VOSS und Stiefel zusammen. Seitdem sind wir sehr zufrieden mit der Produktqualität und dem Service, den wir durch diese Partnerschaft erhalten. Wir wünschen uns, dass das in Zukunft so bleibt“, resümiert Kuhn.
Kleiner Ring – große Aufgabe
Kleiner Ring – große Aufgabe
In weniger als einer Minute nimmt das Spezialfahrzeug Phoenix der Goldhofer Unternehmensgruppe ein Flugzeug auf und transportiert es bei Bedarf gleich mehrere Kilometer über die Rollbahn bis ans Ziel. Dabei können auch Vibrationen entstehen, die eine maximal belastbare Rohrverbindungstechnik erfordern. Bei seinem neuen Flugzeugschlepper vertraut Goldhofer daher ausschließlich auf Komponenten von VOSS Fluid wie leckagesichere, weichdichtende Schneidringe in Kombination mit einem speziellen Vormontagegerät. Eine besondere Bedeutung im Einsatz bei Wind und Wetter und gegen aggressive Enteisungsmittel im Winter kommt zudem dem langzeitsicheren Korrosionsschutz durch die Zink-Nickel-Beschichtung VOSS coat zu.
Der Name Goldhofer steht für robuste und intelligente Transportlösungen im Schwerlast- und Spezialtransport – auf der Straße, Offroad und am Flughafen. Weit über 35.000 Fahrzeuge lieferte das Unternehmen weltweit in mehr als 160 Länder, darunter auch über 6.000 Flugzeugschlepper. Ohne sie wäre der Airport-Betrieb undenkbar, denn auch das modernste Flugzeug kann eines nicht: den Rückwärtsgang einlegen. Genau an dieser Stelle übernehmen die Goldhofer-Fahrzeuge, die die Maschinen exakt in die gewünschte Start- oder Parkposition ziehen und schieben. Brandneu auf dem Markt ist der AST-2P/X, kurz: Phoenix. Die vierte Generation der stangenlosen Flugzeugschlepper ist in der Lage, mehr als 80 Prozent aller weltweit eingesetzten Flugzeuge zu bewegen.
Dazu zählen unter anderem die neue A350 von Airbus sowie die in der Entwicklung befindliche B777X von Boeing. „Geniale Lösungen sind immer einfach. Aber einfache Lösungen zu entwickeln, ist eine große Herausforderung“, bringt es Stefan Fuchs, Vorstandsvorsitzender der Goldhofer Aktiengesellschaft, auf den Punkt. „Mit dem Phoenix wollten wir weg vom allgemeinen Trend des Over-Engineerings. Daher haben wir uns auf das Wesentliche konzentriert und uns auf höchste Verfügbarkeit, verlässliche Technik und minimalen Wartungsaufwand fokussiert.“ Das Ergebnis ist ein komplett neues, kompaktes und modulares Fahrzeugkonzept, das in Punkto Antrieb, Motor, Bremskraft und vielen weiteren Bereichen neue Maßstäbe in Funktionalität und Kundennutzen setzt.
Beispiel Aufnahmevorrichtung
Nur ein wahrer Kraftprotz kann ein voll besetztes und voll betanktes Flugzeug bewegen. Der Phoenix leistet dies, indem er das Bugrad des Flugzeuges mit den Schwenkarmen seiner Aufnahmevorrichtung umschließt, spannt und anhebt. In dieser Position zieht der Schlepper die Maschine bei Bedarf kilometerweit in der auf Flughafenarealen zugelassenen Höchstgeschwindigkeit von 32 km/h. Um das Flugzeug sicher aufzunehmen benötigt der Phoenix weniger als eine Minute – was unter Flugzugschleppern einer Rekordzeit entspricht. Doch Goldhofer ging es bei der Entwicklungsphase nicht nur um eine optimale Performance. Unter der Maßgabe des Lean-Design-Gedankens wurde die Aufnahmevorrichtung komplett neu gestaltet. Waren bei den Vorgängermodellen beispielsweise noch 14 Hydraulikzylinder im Einsatz, kommt der AST-2P/X mit acht Zylindern aus. Das übersichtliche Hydraulikschema bietet freien Zugang zu allen entscheidenden Wartungspunkten. Und entgegen dem Trend, Hydraulikrohre zunehmend durch Schläuche auszutauschen, setzt Goldhofer auf Hartverrohrung.
„Wir verzichten weitgehend auf Schläuche, weil diese sehr wartungsintensiv sind“, erläutert CEO Fuchs. „Rohre hingegen müssen nur zu Beginn vernünftig montiert werden. In Kombination mit zuverlässiger Verbindungstechnik entstehen wartungsarme, leckagefreie Systeme, die über die gesamte Lifetime-Performance unserer Fahrzeuge zuverlässig arbeiten.“ Voraussetzung ist der Einsatz qualitativ hochwertiger Komponenten. Eine besondere Rolle innerhalb des Hydrauliksystems übernimmt dabei die Rohrverbindungstechnik. Hier setzt der Spezialist für Spezialtransportfahrzeuge auf die weichdichtenden Schneidringe ES-4 der VOSS Fluid GmbH. „Unserer Entscheidung für diese Technologie gingen zahlreiche Tests und Eignungsprüfungen voraus“, berichtet Fuchs. „Schließlich ist eine perfekte Hydraulik von Flugzeugschleppern das wichtigste Argument für Funktionalität und Langlebigkeit.“
Hohe Dauerfestigkeit
Die weichdichtenden Schneidringe ES-4 bieten selbst bei kontinuierlicher dynamischer Belastung die von Goldhofer geforderte dauerhafte und sichere Rohrhaltung sowie höchste Leckagesicherheit. Sie kommen an diversen Hydraulikverbindungsstellen des neuen Flugzeugschleppers zum Einsatz, unter anderem am Vormontageschild, einem entscheidenden Bauteil der Bugrad-Aufnahmeeinrichtung. Das Plus an Leckage- und Prozesssicherheit des Schneidrings ist unter anderem auf die ausgeklügelte Zweischneidentechnologie sowie die beiden integrierten Weichdichtungen zurückzuführen. Der Blockanschlag des Systems sorgt darüber hinaus für Übermontageschutz. Durch die Verteilung der Belastung auf zwei Schneiden erhält die Verbindung eine besonders hohe Dauerfestigkeit: Während die erste Schneide für den sicheren Halt des Rohres sorgt, optimiert die zweite Schneide die Ausreißsicherheit bei Druckschlägen und reduziert zudem die Gefahr von Leckagen auf ein absolutes Minimum. Der im Körper des Schneidrings integrierte Federeffekt verhindert zusätzlich Nachsetzerscheinungen, die durch Vibrationen entstehen könnten. Selbst lang anhaltende Vibrationen, wie sie beim kilometerlangen Abschleppen eines Flugzeuges entstehen können, wird auf diese Weise wirksam standgehalten.
Im Sekundärbereich des Schneidrings befinden sich zwei vollgekammerte Weichdichtungen aus FPM. Sie dichten die beiden möglichen Leckagewege zum Rohr und zum Stutzen zusätzlich ab für den Fall, dass Hydraulikflüssigkeit die metallische Dichtung überwinden sollte. Eine besonders hohe Langzeitstabilität der Elastomere gewährleistet VOSS Fluid sowohl durch die Materialauswahl als auch durch die geschützte Platzierung der gekammerten Weichdichtungen innerhalb des Schneidrings.
Prozesssichere Montage
Bezüglich der Vor- und Endmontage forderte Goldhofer maximale Prozesssicherheit. Nicht zuletzt, weil sich statistisch mehr als 90 Prozent aller Leckagen von Verschraubungen auf Fehlmontagen zurückführen lassen. Der Spezialist für Spezialtransportfahrzeuge entschied sich daher für die Anschaffung mehrerer Vormontagegeräte der neusten Generation: Der Typ 90 Comfort von VOSS Fluid arbeitet mit Fehlererkennung und automatischer Druckeinstellung. So werden fehlende oder falsch eingelegte Schneidringe schon vor der Montage identifiziert sowie Über- und Untermontagen wirksam unterbunden.
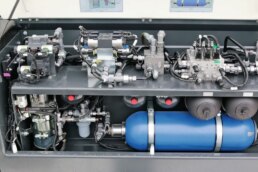
Die Monteure bei Goldhofer rüsten das Vormontagegerät lediglich mit dem passenden verschleißfesten VOSS Werkzeug, das standardmäßig mit einem RFID-Chip ausgestattet ist. Das ins Typ 90 Comfort integrierte RFID-Lesegerät liest den Chip aus und stellt die entsprechenden Montageparameter automatisch ein. Direkt im Anschluss beginnt die prozesssichere und zudem äußerst zügige Vormontage. Auch die Endmontage ist sicher gestaltet, da der ES-4 Schneidring auf Blockanschlag montiert wird. Der deutliche Kraftanstieg signalisiert dem Monteur eindeutig den Endpunkt der Montage. Zum Abschluss markiert der Goldhofer-Mitarbeiter die Verschraubung mit einem gelben Kreuz – jedes Mal ein Zeichen für eine weitere perfekte Verbindung.
Langzeitkorrosionsschutz
Da Flugzeugschlepper bei allen Wetterbedingungen zum Einsatz kommen und im Winter sogar besonders aggressiven Enteisungsmitteln ausgesetzt sind, waren die Forderungen von Goldhofer auch im Hinblick auf den Korrosionsschutz kompromisslos. „Alle unsere Systembauteile sind mit höchstem Korrosionsschutz ausgelegt. Das muß natürlich auch für die Rohrverschraubungen gelten“, berichtet Fuchs. „Damit ist das gesamte System widerstandsfähiger gegenüber mechanischer Beanspruchung und gegenüber aggressiven Medien.“ Für den neuen Phoenix bedeutet dies: Sämtliche Hydraulikleitungen sind galvanisch verzinkt und erhalten eine zusätzliche organische Schutzschicht. Und auch die Rohrverschraubungen verfügen über einen besonderen Zink-Nickel-Oberflächenschutz. Im Fall der ES-4-Schneidringe ist dies der Langzeitkorrosionsschutz VOSS coat. Er erreicht nicht nur die höchste Korrosionsbeständigkeitsklasse K5 nach dem VDMA-Einheitsblatt 24576, sondern überschreitet ebenfalls die geforderten Beständigkeitswerte gegen Weiß- und Rotrost deutlich. „Die ES-4 Schneidringe erfüllen unsere hohen Erwartungen zu einhundert Prozent“, resümiert CEO Fuchs zufrieden. „In VOSS Fluid haben wir einen absolut qualitätsorientierten Partner, auf den wir uns jederzeit verlassen können.“